Напечатать недостающее.
Что такое аддитивные технологии и как их используют на «Томскнефтехиме»
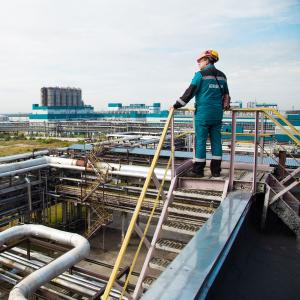
На больших промышленных предприятиях, где работа кипит круглые сутки, нередко возникает потребность в комплектующих для оборудования. И удовлетворить её можно по-разному.
Что-то приобретается у поставщиков, что-то ремонтируют своими силами на производстве. В СИБУРе пошли дальше. Недостающие детали для оборудования производств здесь начали печатать на 3D-принтере.
В нашем материале рассказываем, что такое аддитивные технологии, как они упрощают жизнь на производстве и что обычно печатают в ремонтном цехе «Томскнефтехима».
Создавать новое
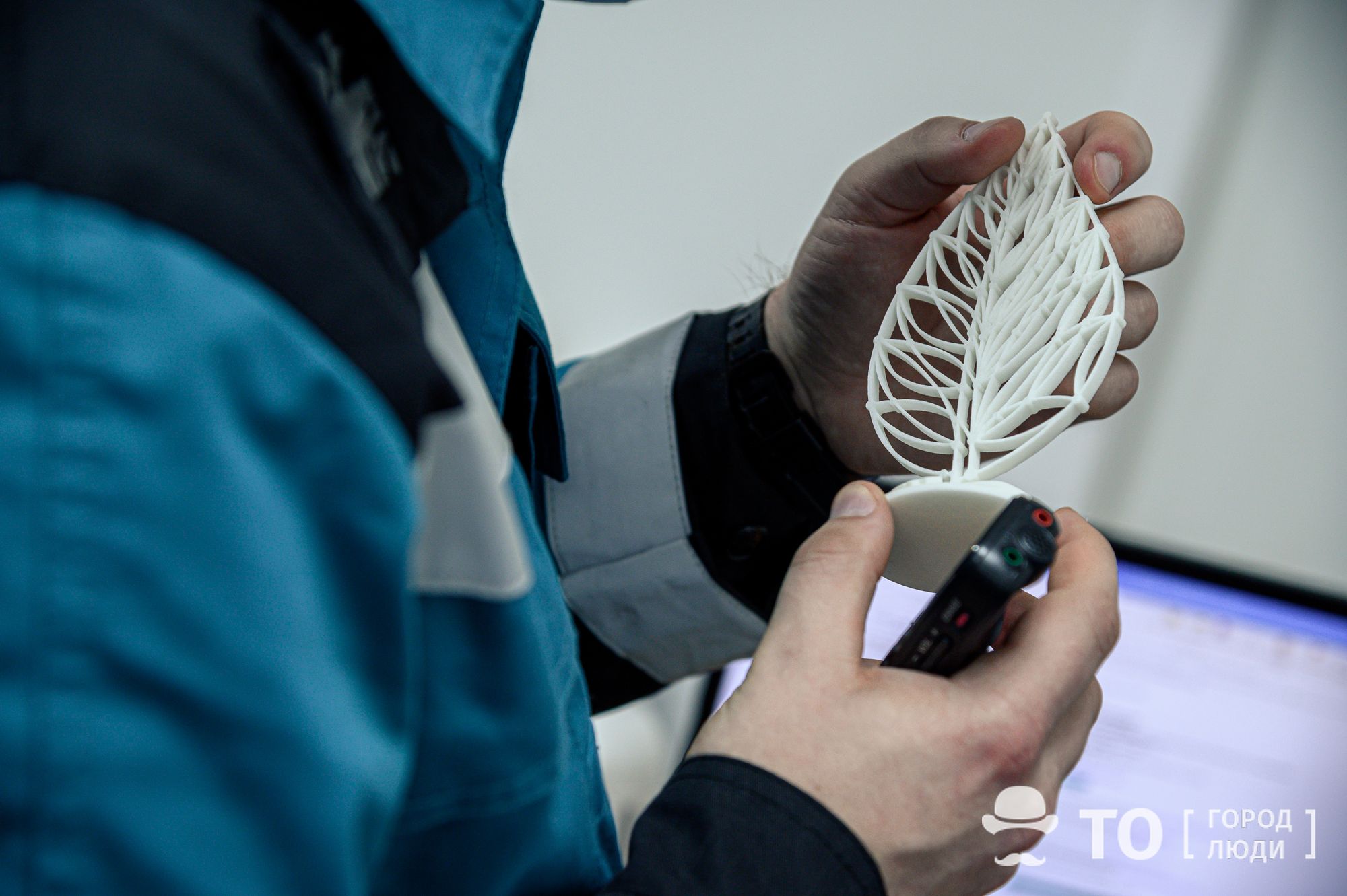
Аддитивные технологии (Additive Manufacturing, также известное как 3D-печать) — это технологии послойного наращивания и синтеза объектов. Отчасти они противопоставляются классическим технологиям производства, которые предполагают создание нового путём отсечения ненужного. Например, чтобы выточить деталь с помощью фрезы необходимо взять заготовку и отрезать лишнее. В случае с 3D-печатью образуется куда меньше отходов, а сырье используется более эффективно. Кроме того, аддитивная печать позволяет добиться гибкости и уникальности изделий — сделать одно, два или три изделия. На «Томскнефтехиме» аддитивные технологии начали внедрять в августе 2019 года.
Печать 3D — это цифровой тренд в нефтехимической отрасли. И аддитивные технологии сегодня являются частью большой цифровой трансформации всей компании СИБУР, и «Томскнефтехима», в частности. Цифровая трансформация позволяет повышать не только эффективность и производительность, но и безопасность технологических процессов, квалификацию сотрудников, снижать объем рутинного труда. В результате фокус смещается на скорость принятия решений.
В 2020 году с помощью аддитивных технологий в СИБУРе изготовлено более 14 тысяч различных деталей для предприятий компании в регионах присутствия. В среднем это позволило в 4-8 раз сократить срок их поставки и, как следствие, время проведения ремонтных работ, а также сэкономить более 50 млн рублей на приобретении и доставке.
— Аддитивные технологии — это ведь не только 3D-печать, но и сканирование, разработка моделей и доработка деталей с помощью специального программного обеспечения. Запчасти, которые мы печатаем своими силами, обходятся дешевле, чем мы покупали бы на рынке. Второй плюс — это скорость. Сроки поставки деталей могут доходить до полугода, а мы напечатаем эту деталь за две-три недели, — поясняет главный инженер «Томскнефтехима» Роман Жалюк.
Сегодня в СИБУРе работает восемь центров по развитию аддитивных технологий, в том числе в Томске. Новое подразделение разместили на площадях централизованного ремонтного производства. Рядом расположены станки, на которых можно обрабатывать детали.
— Я работаю на предприятии с 2011 года. Сначала был инженером-конструктором, а два года назад мне предложили заняться аддитивными технологиями. Стало любопытно — это новая для меня область. Прошёл обучение по сканированию — в Москве в IQB, — рассказывает инженер Виктор Голик. — Производство занимается ремонтом основного оборудования. Поэтому логично, что и аддитивные технологии сосредоточены здесь.
Печать в пространстве
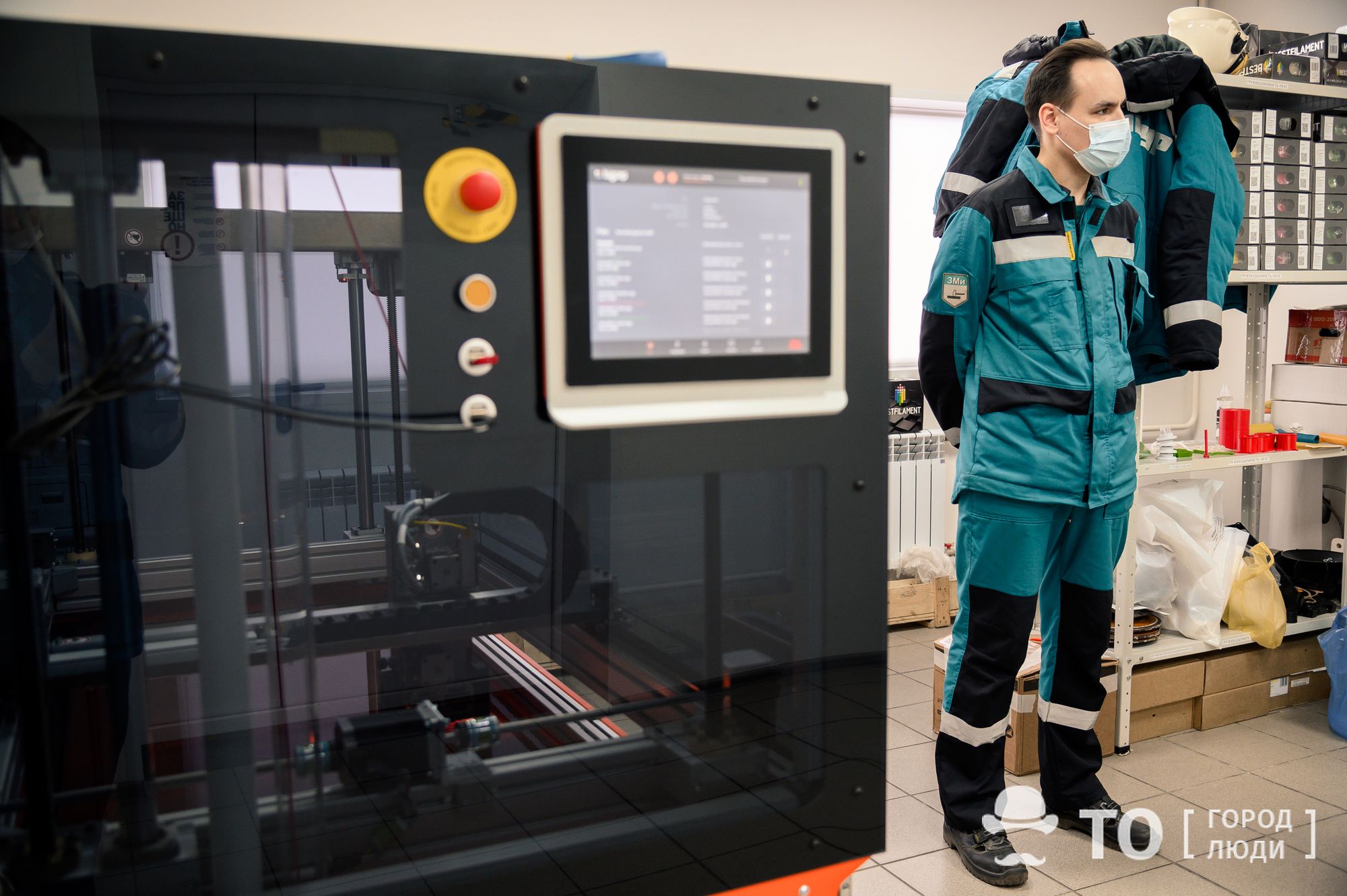
Сердце отдела аддитивных технологий — большой немецкий 3D-принтер. Он представляет из себя специальную камеру в которой по трём осям (вверх-вниз, вправо-влево, вперёд-назад) двигается каретка. В нее подается исходный материал: своего рода толстая леска из разных полимеров (полиэтиленгликоля, полилактида или термополиуретана), которая разогревается до 225 градусов. Расплав выдавливается из каретки: двигаясь согласно программе, она тонкими слоями выкладывает расплавленный пластик на разогретый до 70 градусов стол, покрытый специальным материалом (чтобы изделие лучше держалось).
На одну небольшую деталь уходит около часа работы. При этом одновременно принтер может печатать несколько десятков необходимых конструктивных элементов. После печати каждая деталь требует небольшой доработки — на ней могут оставаться швы, которые легко срезаются и шлифуются.
СИБУР, как один из крупнейших производителей полиолефинов, заинтересован в расширении областей использования полипропилена, в том числе в сфере аддитивных технологий. Известными преимуществами полипропилена в этой сфере является его химическая стойкость, лёгкость, что расширяет области возможного применения напечатанных изделий. Сегодня наша R&D-команда работает над разработкой полипропиленовых материалов для 3D-печати. Уже получены положительные результаты испытаний разработанной нами полипропиленовой композиции от потребителей.
— Сейчас мы печатаем из полиэтиленгликоля. У нашего принтера низкая температура платформы, что ограничивает номенклатуру материалов. Печатаем из полилактида — это биоразлагаемый материал, который производится из молочной кислоты, кукурузы, кукурузного и картофельного крахмала. Конструктивные изделия из него печатать сложно, но можно делать кожухи, крышки, которые не несут конструктивной нагрузки, — рассказывает Виктор Голик. — Из термополиуретана делаются гибкие изделия. Мы печатаем им демпферы (устройства для гашения вибрации). Полумуфты, детали для передачи вращающего момента и прочие конструктивные изделия изготавливаются из полиэтиленгликоля. Оригинальные детали производят с помощью пресс-формы методом вулканизации. У нас это делается без пресс-формы.
Материалы, которые используют для печати на «Томскнефтехиме», местные, их производят в посёлке Зональный. Здесь научились делать отличные полимерные нити. Томские производители сырья для 3D-принтеров даже открыли отделение в Германии. Материалы поставляются в виде катушек. Детали из полимеров получаются лёгкими, поэтому одной катушки хватает надолго.
Искусство моделирования
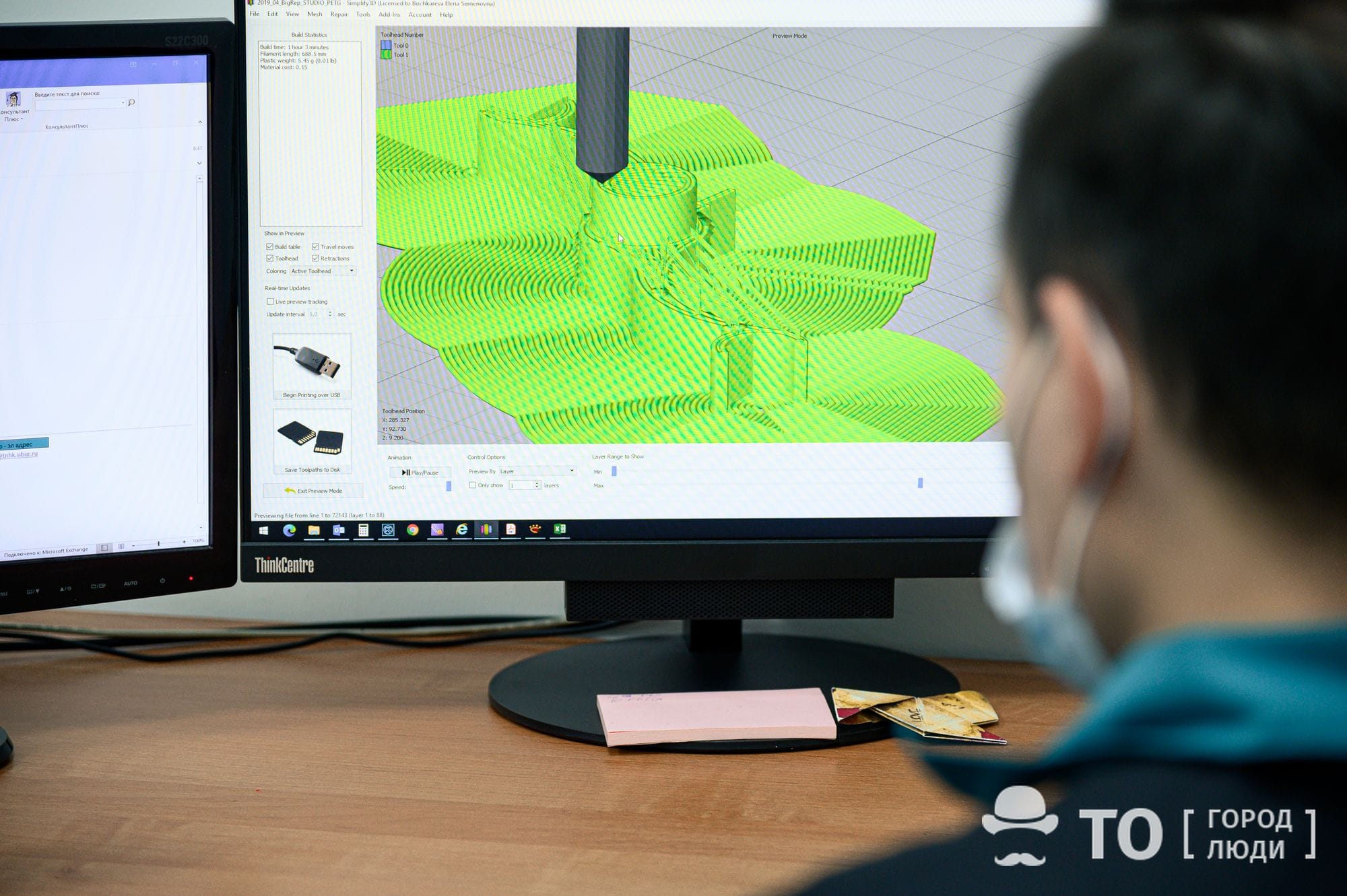
Мозг отдела аддитивных технологий — инженер и специальное программное обеспечение, в котором он готовит 3D-модели будущих изделий.
— Я занимаюсь подготовкой деталей — по чертежам или образцам, — рассказывает Виктор Голик. — У нас идёт полный цикл воспроизводства. Не просто «изготовили, отдали и забыли». Мы собираем информацию, опытно-промышленная эксплуатация проходит для принятия решения о замещении детали в наших продуктивных системах. Например, мы можем отказаться от закупки каких-то деталей, если понимаем, что можем произвести их сами. Может быть и наоборот, когда напечатанная деталь нас не удовлетворила. Или вопрос в цене — иногда изготовить что-то самим гораздо выгоднее.
Подготовка моделей — отдельное искусство. Некоторые из них можно изготовить по имеющимся чертежам, где-то можно измерить посадочные места и прикинуть габариты будущего изделия. Однако бывают и более сложные элементы, которые нельзя просто перенести в понятную для 3D-принтера твердотельную модель. Тут на помощь инженеру приходит 3D-сканер, который представляет собой проектор с двумя камерами. Он освещает исходную деталь, покрытую специальной краской (мелкодисперсный мел, смешанный с изопропиловым спиртом) и метками. Камеры ловят преломление света и создают виртуальный оттиск видимой части изделия. После первой подобной «фотосессии» деталь поворачивают и снова «снимают». В итоге из таких цифровых слепков получается довольно точная 3D-модель, которую уже можно передавать на печать. Также сканер приходит на помощь, если образец для нужной детали повреждён.
— Самое крупное, что нам довелось изготавливать, — это кожух для электродвигателя. Он стоит на заводе «Биаксплен». Оригиналы металлические и выполняются штамповкой. Мы его напечатали — он 380 мм в диаметре и 400 мм высоту. Кожух не несёт конструктивной нагрузки, просто защищает вентилятор, охлаждающий электродвигатель, от попадания крупного абразива, а персонал — от вращающихся частей. На его печать ушло около 60 часов, — рассказывает Виктор Голик.
150 заказов на 2020 изделий
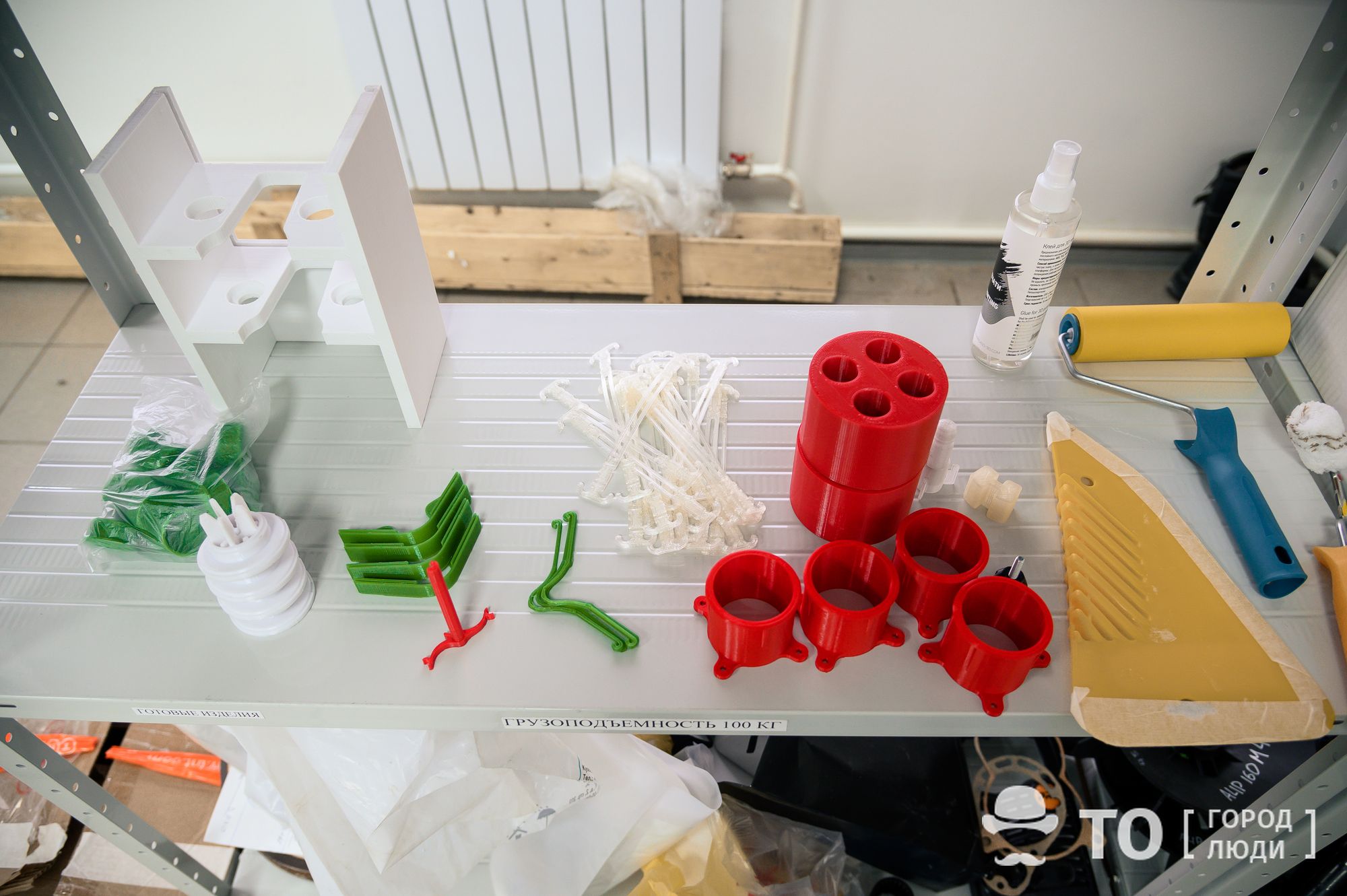
Для того, чтобы новая технология производства деталей прижилась на производстве, потребовалось некоторое время.
Поначалу в отдел аддитивных технологий обращались пару десятков раз. На сегодняшний день у инженера 3D-печати «Томскнефтехима» 150 заказов на 2020 изделий. И это только плановая потребность, не включающая внезапные и экстренные задачи.
Точнее, тверже, быстрее
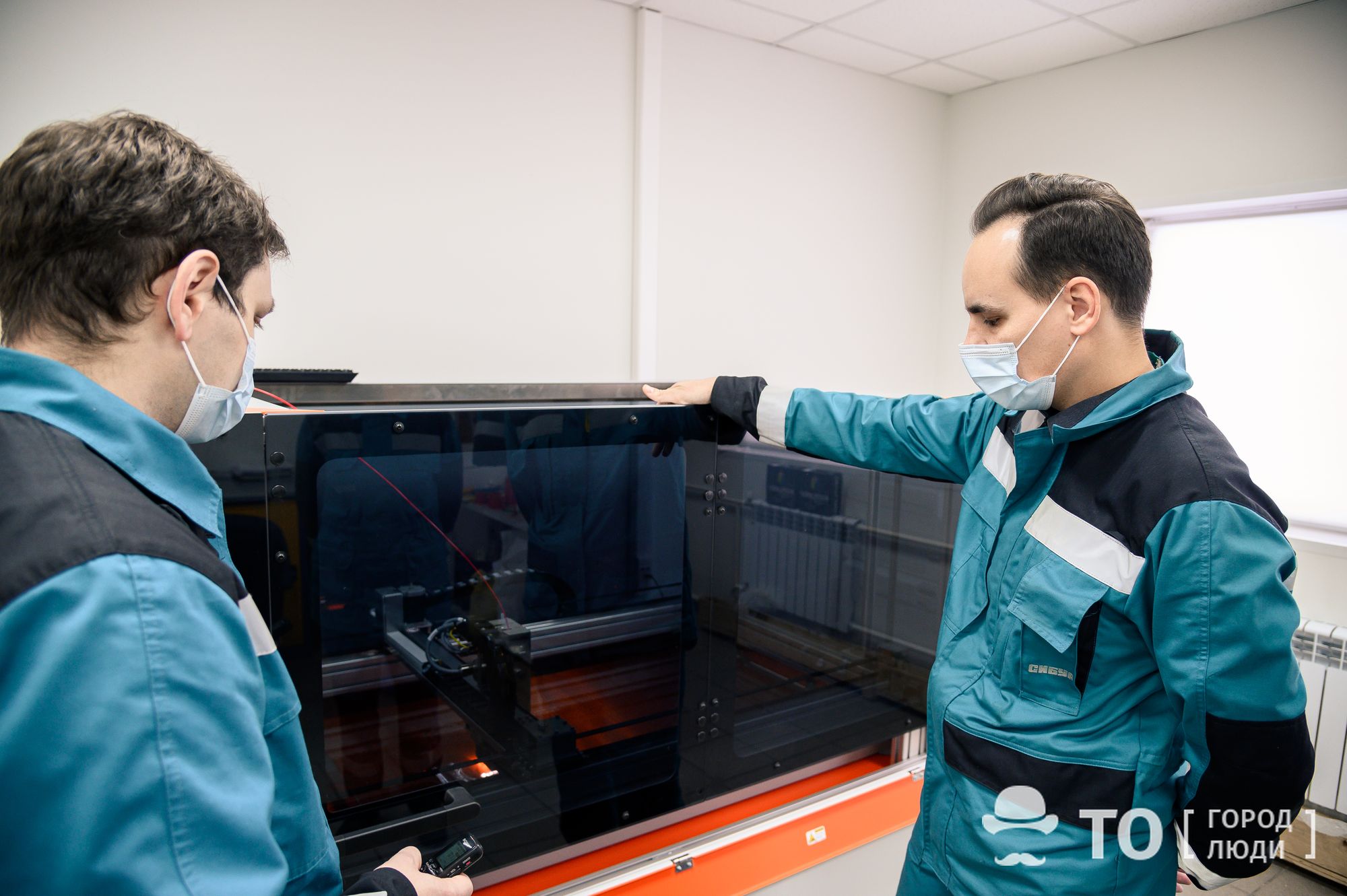
В августе в отделе аддитивных технологий появится еще один 3D-принтер — поменьше и поточнее. С его помощью можно будет печатать композитными материалами, например, угле- или стеклонаполненными пластиками. Они прочнее, чем те, из которых детали печатаются сейчас. Таким образом, возможности применения аддитивных технологий расширятся для всех томских предприятий СИБУРа.
Аддитивные технологии, к которым в том числе относится 3D-печать, неспроста включены в перечень сквозных технологий. Потому как они проходят через все существующие отрасли, и те, которые в будущем появятся в нашей жизни.
Сегодня аддитивная печать активно входит в медицину — вплоть до того, что сегодня спортсменам изготавливают индивидуальную обувь, печатая резиновые подошвы строго под форму ног. Печать имплантатов становится одним из перспективных направлений развития, потому что импланты никогда не повторяются и другими технологиями их изготовить нельзя.
Аддитивные технологии появились в строительстве зданий — большие установки фактически льют бетон послойно. И это позволяет каждый раз архитектору рисовать новый проект, он всегда будет изготовлен в уникальном экземпляре.
На мой взгляд, аддитивные технологии очень недооценены, и в ближайшее время произойдёт просто колоссальный бум их развития. Они будут внедряться повсеместно, и чем скорее мы начнём их осваивать, разрабатывать новые на их базе, тем больше шансов у нас совершить больший вклад в развитие экономики страны.
Подробнее узнать о других цифровых инструментах, успешно применяемых на «Томскнефехиме», можно здесь.
Текст: Егор Хворенков
Фото: Серафима Кузина, пресс-служба СИБУРа
Подписывайтесь на наш телеграм-канал «Томский Обзор».