На пути к индустрии 4.0. Цифровизация на «Томскнефтехиме»
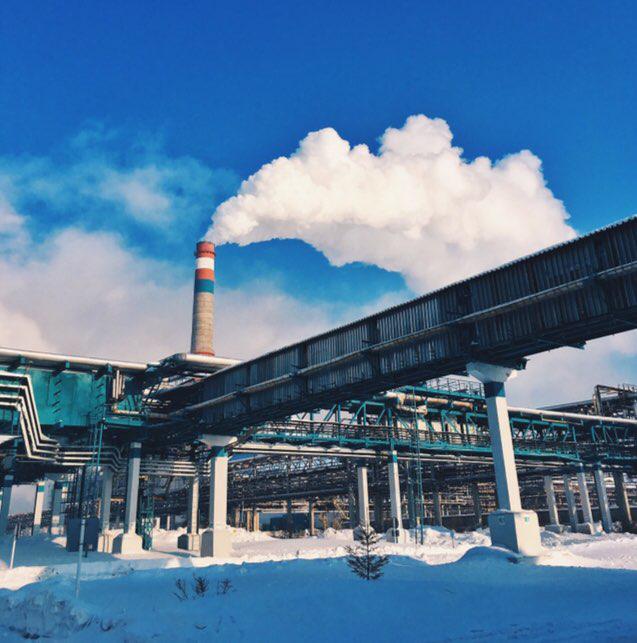
В условиях пандемии цифровые инструменты влияют на повышение производительности труда и обеспечивают устойчивую работу предприятий в целом. Возможность организовать удаленную работу, автоматизация производственных процессов — все это не только облегчает жизнь, но и влияет на безопасность работников. Мы спросили экспертов, зачем производствам автоматизация, а также на примере «Томскнефтехима» узнали, какие современные технологии внедряются на предприятии сегодня.
В долгосрочной перспективе автоматизация и цифровизация производства напрямую влияет на повышение производительности труда, эффективности производства, создание комфортных условий труда для работников. Есть и синергетические эффекты, которые в итоге приводят к повышению экономических показателей.
Однако в краткосрочной перспективе автоматизация — весьма затратный процесс, требующий усилий не только от разработчиков, но и руководства предприятия, персонала. Переходный процесс внедрения любого вида автоматизации даже на самом динамичном производстве занимает не менее полугода. Управленческий корпус должен это понимать и держать ориентир на долгосрочные перспективы.
Во главе идеологии Индустрии 4.0 стоит создание цифровых моделей технологических производств, которые позволяют достигать качественно нового уровня управления предприятием на всех уровнях.
На производствах СИБУРа процесс цифровизации и автоматизации начался задолго до пандемии. И в производственный процесс томского предприятия сегодня уже прочно вошли система «Эконс», интернет вещей, цифровые наряды-допуски, мобильные обходы, системы видеоаналитики и советчики. Подробнее о некоторых из этих технологий — далее в нашем материале.
Мобильные обходы
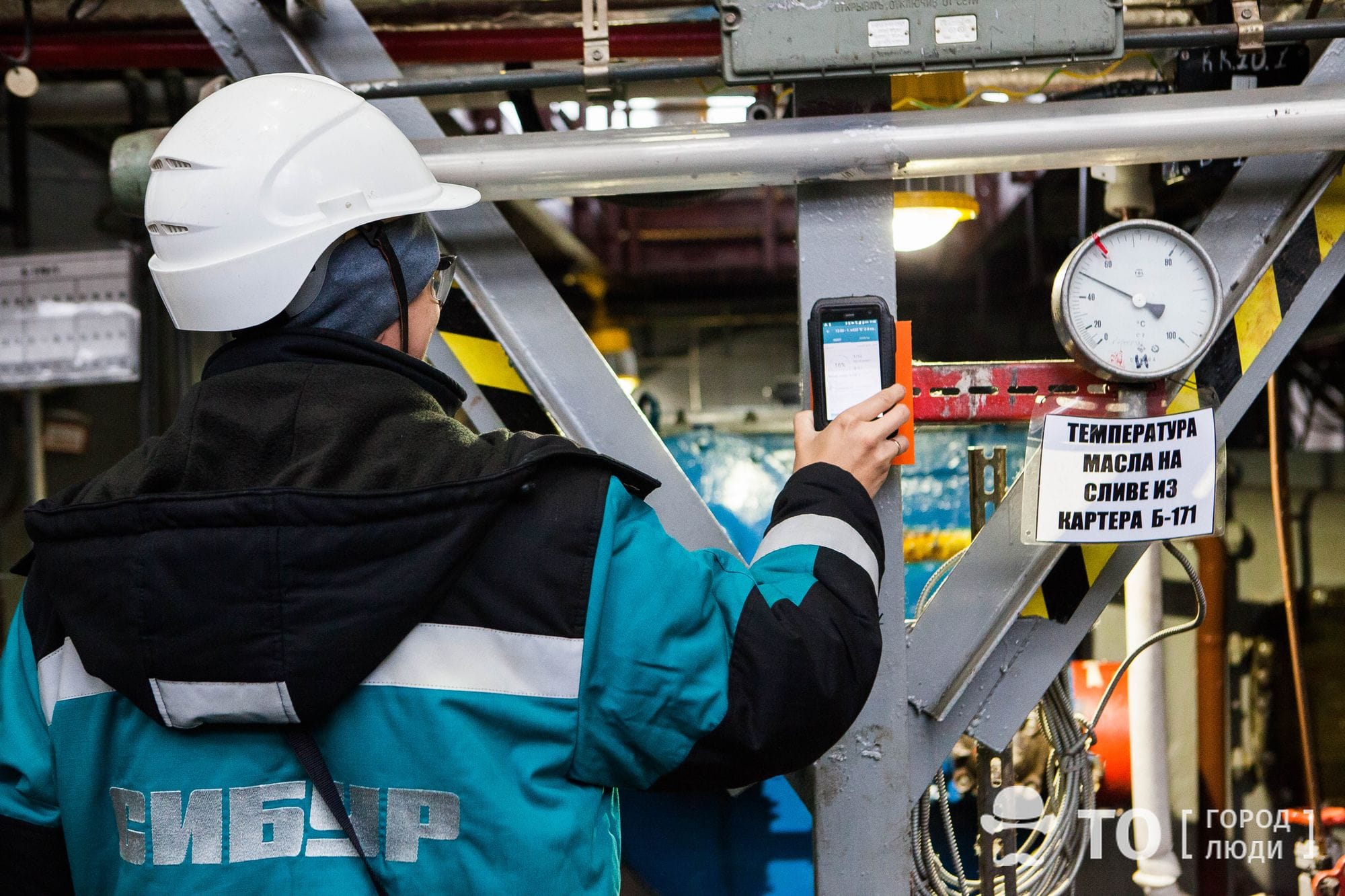
На «Томскнефтехиме» аппаратчики и машинисты пользуются цифровым инструментом «Мобильные обходы» при ежесменном контроле за состоянием технологического оборудования. Это комплексное решение, которое включает в себя web-среду, мобильные устройства и NFC-метки (Near Field Communication).
Все это работает следующим образом: работник производства, в задачи которого входит ежедневная проверка оборудования, получает мобильное устройство, подключенное к системе (адаптированный под определенные цели смартфон). В гаджете записан маршрут, по которому работник должен выполнять обход. По пути следования рядом с различным технологическим оборудованием размещены специальные метки. Подойдя к ним, специалист фиксирует их, оценивая состояние оборудования.
Информация попадает в систему и передается начальнику смены. Тот, в свою очередь, оформляет заявку на устранение возможных неполадок и направляет ее сервисным службам. Кроме того, с помощью этого инструмента можно давать задания обходчикам.
«Если раньше мы отслеживали, как персонал проверяет оборудование через бумажные носители-чеклисты по местам, журналы регистрации дефектов, то сейчас у нас все это через цифровой инструмент — мобильные обходы — отображается онлайн. Какие метки и когда посещались, какие дефекты по данному оборудованию были выявлены, в какой срок они были устранены. Полная прозрачность, — отмечает начальник установки катализаторов и подготовки сырья производства полипропилена Александр Чертенков. — И самое главное — визуализация. Мы сейчас можем понять, в чем характер дефекта, не только по устному или письменному описанию. Увидев фотографию оборудования, уже можно первичным образом организовать работы по устранению поломки, не выходя на место. Самое дорогое в нашей жизни — это время. И чем меньше мы его тратим, тем эффективней мы работаем».
Доступ к приложению имеет весь инженерно-технический персонал, вплоть до руководителей производства. Все они могут в режиме реального времени следить за тем, как проверяют оборудование и в каком состоянии оно находится.
«Заступая на смену, мы видим перечень маршрутов для конкретного обходчика и время, когда он должен совершить обход, — рассказал Сергей Озеров, руководитель единой службы технического заказчика. — В зависимости от степени автоматизации обходы могут быть чаще или реже. Повышая уровень автоматизации производств, мы сокращаем обходы».
Сегодня на «Томскнефтехиме» в работе находится 121 мобильное устройство. Еженедельно с ними совершается 4200 обходов оборудования. Мобильные обходы и сегодня совершенствуются командой разработчиков, которые принимают предложения по ее доработке у пользователей.
Кстати, о разработке этого цифрового инструмента в СИБУРе сняли игровой мини-сериал «Прототип», где в основу сюжета легли реальные рабочие процессы.
€kon$: тонны в деньги
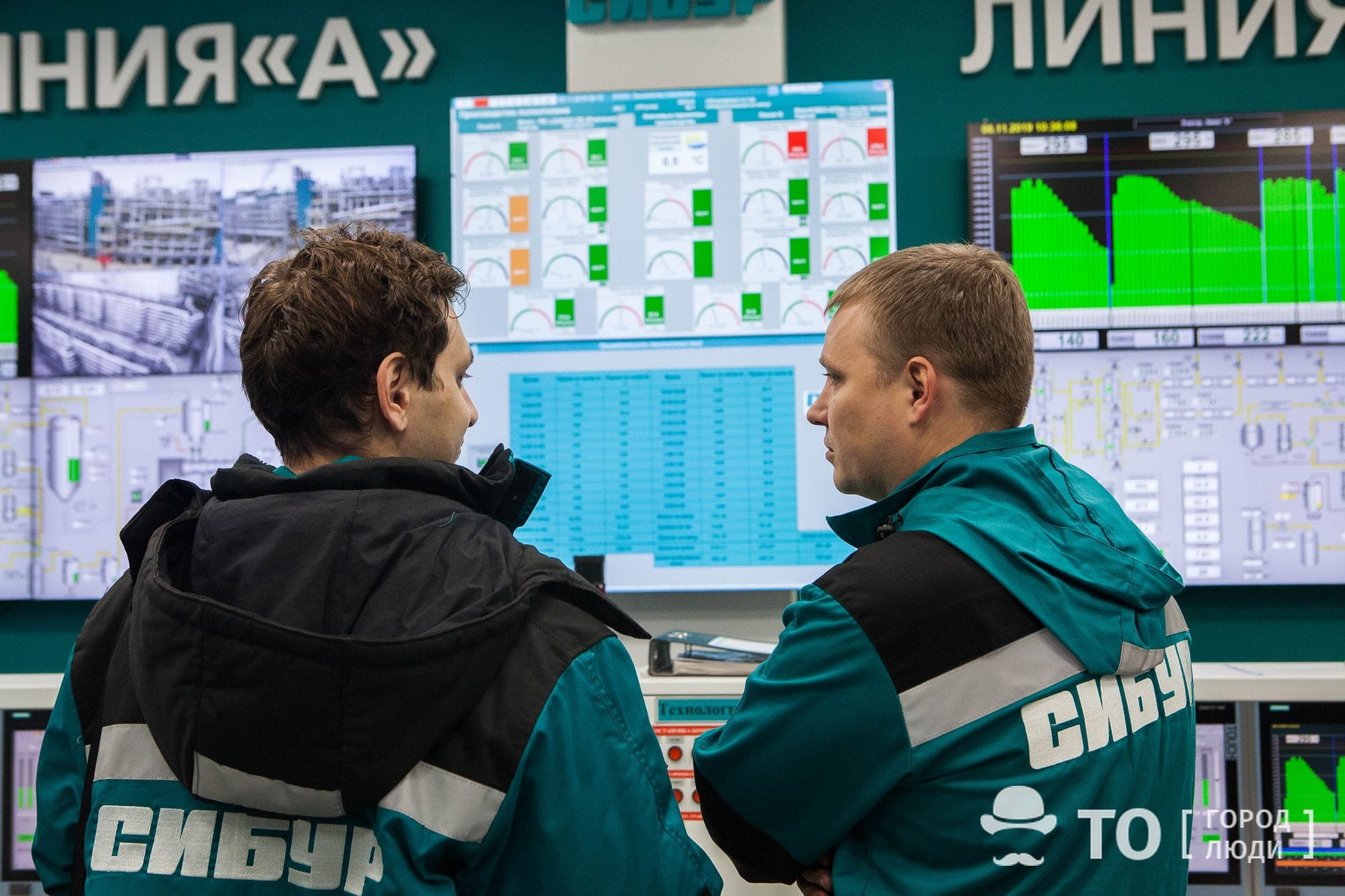
На нескольких производствах «Томскнефтехима», а именно на производствах мономеров, полипропилена и полиэтилена, в этом году появились экраны, преобразующие производственные показатели в деньги. Система под названием «Эконс» призвана мотивировать персонал, наглядно показывая вклад работников каждой смены в большое общее дело.
«У нас каждый продукт имеет свою стоимость на рынке. Мы знаем свои затраты на сырье. Все это трансформировано в нашем инструменте. Тот пар, который мы потребляем, тот этилен, который мы выпускаем, — здесь как раз отображаются тонны, пересчитанные в рубли. Это непосредственная мотивация работать хорошо с точки зрения производительности и качества выпускаемого продукта», — рассказывает начальник производства полиэтилена Дмитрий Тимошенко.
В практическом приложении система представляет собой большую панель, на которую выведены несколько десятков различных показателей. Она находится в центральном пульте управления производства, где ее могут видеть операторы. Например, на ЦПУ производства полиэтилена панель включает несколько «спидометров» идентичных для двух линий: производительность, качество, расход сырья, а также общие для двух линий показатели: температура оборотной воды, захоложенного конденсата, удельный расход этилена, пара и азота.
«В чем плюс того, что „Эконс“ находится на ЦПУ — это то, что человек, который сидит за пультом, может регулировать производственные процессы и видеть, какой экономический вклад он приносит предприятию», — рассказал начальник производства полиэтилена Дмитрий Тимошенко.
На производстве мономеров «Эконс» выглядит более сложно. В зале ЦПУ размещено целых семь экранов со своими метриками, ведь здесь получают гораздо больше товарной продукции: этилен, пропилен, а также побочные: бутилен-бутадиеновая фракция, смесь ароматических углеводородов и тяжелая пиролизная смола. Операторы отмечают, что с введением «Эконс» они стали более наглядно видеть показатели производительности и энергоэффективности, а также оперативнее реагировать на их изменения.
Если раньше персонал предприятия жил в парадигме тонн и килокалорий, то сейчас каждый производственник понимает, сколько те или иные действия приносят дополнительного маржинального дохода или, наоборот, заставляют его упускать.
Первое предприятие СИБУРа, где внедрили «Эконс» — нефтехимический завод в Кстово. Разработку и развертывание этого инструмента выполнял внешний подрядчик. Одновременно они обучали работе с системой сотрудников СИБУРа, в том числе томичей.
Умные камеры
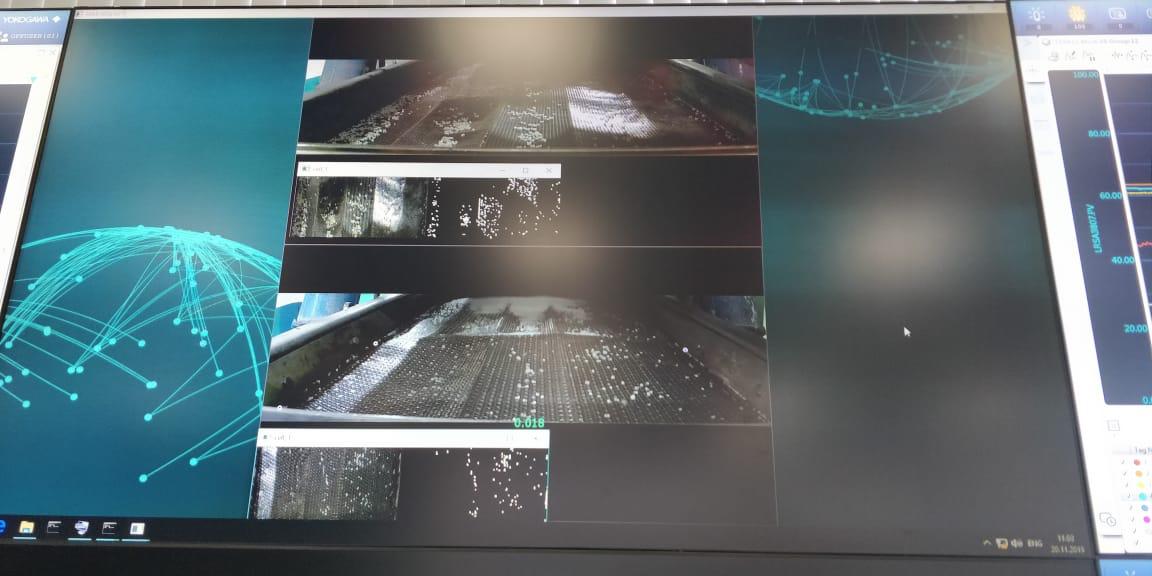
Еще одной частью будущей цифровой инфраструктуры станут интеллектуальные системы видеоаналитики. Одну такую как раз тестируют на установке гранулирования полипропилена. Две «умные» камеры следят за тем, чтобы гранулы полипропилена, потоком выпадающие из экструдера (своего рода мясорубки) правильно распределялись на кондиционные и некондиционные. Для этого систему специально калибровали — буквально показывали ей, какое количество и форма гранул говорит о нормальной работе экструдеров, и когда необходимо принимать меры. Сейчас изображение с экструдеров выведено на большую панель, и аппаратчики могут проверять, работает ли система. Причем картинка неполадки появляется, только тогда, когда система фиксирует отклонение, и требуется вмешательство человека, а когда же все штатно — экран работает в спящем режиме, не отвлекая на себя внимание оператора.
Цифровой советчик
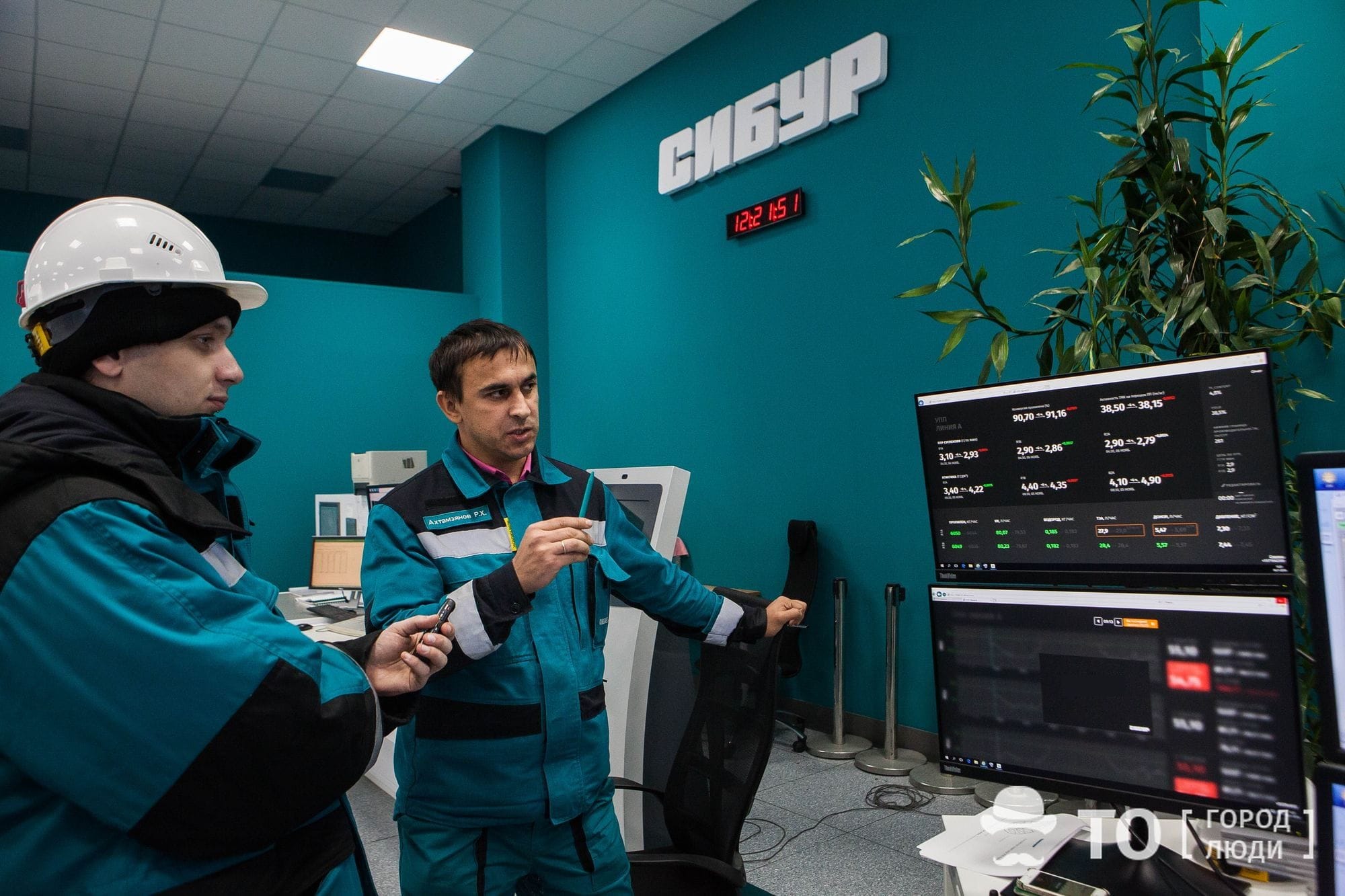
Не только «умные» камеры, описанные выше, обладают подобием интеллекта. На установке полимеризации аппаратчикам помогает «Умный помощник». Это обучаемая система, которая с точностью более 90% может предсказать значения рабочих параметров оборудования через 6 часов.
Система строит прогнозы на основе данных, которые передаются с АСУТП (автоматизированная система управления технологическим процессом). Грубо говоря, помощник видит те же цифры, что и операторы, однако, в отличие от людей, он может учитывать и обрабатывать их все, формируя прогноз.
«Важна не только конечная выработка порошка, но и стабильность режима, а также снижение атактической фракции, повышение активности и конверсии. Эти три основных составляющих советчика, которые зашиты в математической модели. Для их просчета через математические прогнозные модели проходят порядка 60 различных показателей», — объясняет менеджер инженер-технолог ПЭ Раис Ахтамзянов.
Интерфейс системы состоит из двух частей. Верхняя часть, прогнозная, показывает, какими могут стать ключевые показатели производительности через шесть часов при сохранении текущих параметров установки. Нижняя часть — рекомендательная. Она предлагает изменить некоторые параметры, чтобы добиться оптимальной работы установки. При этом система учитывает зашитые в нее большие данные за предыдущие периоды времени. Именно на эти показатели могут опираться операторы при регулировании режима работы установки.
«На основе исторических данных модель знает, какие основные регулирующие параметры на каждый реактор нужно поддерживать, чтобы получить целевой ПТР (показатель текучести расплава), повысить конверсию, активность и снизить атактику по возможности. Самое главное — большая выработка конечного продукта и стабильность режимов», — отмечает Раис Ахтамзянов.
«Цифровые инструменты у нас разрабатываются собственной командой разработчиков. В СИБУРе не пошли по пути закупки „коробочных решений“, а наняли исполнителей. Разработчики всех цифровых инструментов, которые тиражируются по всем нашим предприятиям, находятся в компании „СИБУР Диджитал“», — отметил Сергей Озеров.
Автоматизация и цифровизация производств «Томскнефтехима» — процесс непрерывный и постоянно совершенствующийся. Все это часть большой работы по цифровой трансформации, начатой СИБУРом несколько лет назад. В компании убеждены, что цифровая трансформация обеспечит дополнительные возможности для сотрудников, снизит объем рутинного труда за счет роботизации, повысит безопасность рабочих процессов.
Автоматизация в промышленности применяется уже давно. Крупные компании, которые работают на мировых рынках, просто вынуждены были повышать свою эффективность за счет систем автоматизации, чтобы соответствовать стандартам этих рынков.
Сейчас все говорят уже не про автоматизацию, а про цифровизацию производства. Если автоматизация — это документооборот, съем данных с датчиков и так далее, то цифровизация — это комплекс данных: как внешних, так и внутренних, производственных. Их сбор и анализ позволяет принимать более качественные управленческие решения. Так как производственная цепочка становится прозрачной и каждый ее узел оцифрован, то появляются скрытые возможности для роста или выявляются проблемные моменты, на которые можно точечно воздействовать и повышать эффективность.
В будущем цифровизация станет неотъемлемой частью производства. Если у тебя нет цифровизации — ты за рынком. При этом масштабного сокращения рабочих мест, конечно же, не будет. Потому что сколько до этого было промышленных революций? А людей все больше, и у всех есть работа. Это всего лишь очередной этап повышения эффективности и перехода человечества на другой уровень работы.
Пандемическая ситуация показала, что переход может быть очень быстрым. До этого годами говорили о том, что роботизация растет, надо людей переучивать, целые программы писались. Но вот за три месяца все произошло. Открылось неограниченное количество онлайн-университетов и курсов по любым специальностям, и человек из любой отрасли может за 2-3 месяца даже бесплатно найти себе источник компетенций и переквалифицироваться. Так и переход к цифровизации может произойти практически мгновенно.
Текст: Егор Хворенков