Нефтехим. БОПП-пленка: упаковка для всего
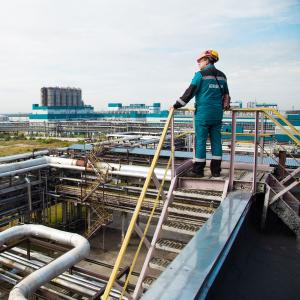
Вы купили в магазине пельмени, пряники или крупы? Все они упакованы в БОПП-пленку. Заклеили коробки для переезда скотчем? Он сделан из БОПП-пленки. Получили на день рождения букет цветов в эффектной тоненькой упаковке и фольгированный воздушный шар? Они тоже изготовлены из БОПП-пленки.
Во втором материале нашего спецпроекта рассказываем о том, как в Томске «растягивают» гранулы полипропилена, чтобы получить легкую, прочную и доступную упаковку для всего.
Дитя полипропилена
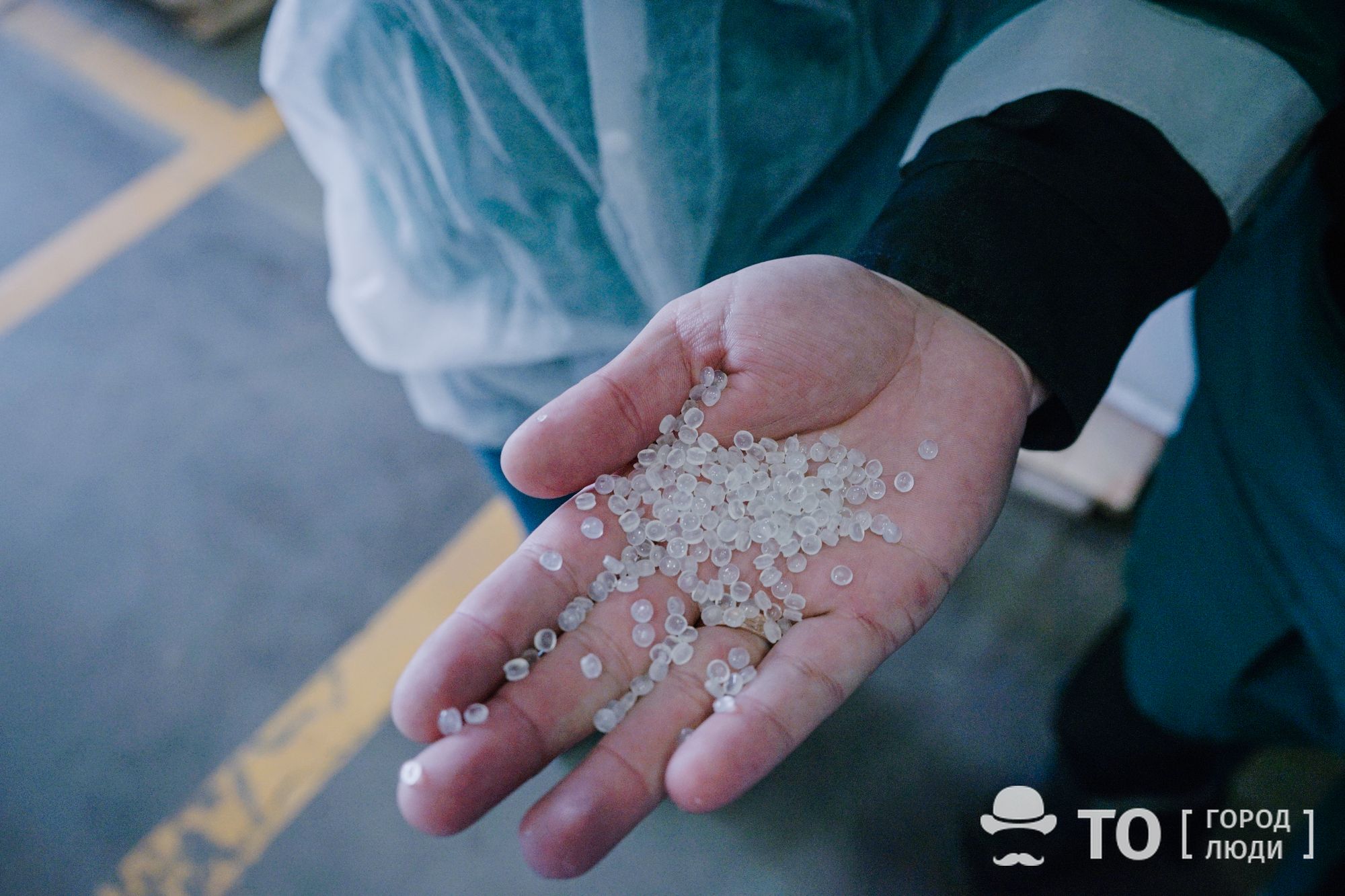
Биаксиально-ориентированную полипропиленовую пленку (так расшифровывается БОПП) делают из полипропилена.
От своих полимерных собратьев — других пленок из полипропилена и полиэтилена — БОПП отличается большей эластичностью. Это надежная упаковка, но при этом ее легко «распаковать», и это не недостаток. Благодаря ее свойствам такую пленку часто используют для упаковки продуктов и не только: представьте, как неудобно было бы разрывать полиэтиленовый пакет! А с БОПП потребуется пара небольших усилий, и макароны из пачки уже отправляются в кастрюлю.
Более того, процесс создания БОПП-пленки позволяет получать материал с самыми разными свойствами. Его можно сделать прозрачным или непрозрачным, укреплять и украшать, придавать металлический блеск и наносить любой рисунок.
Для упаковки продуктов сегодня это, пожалуй, эталонный материал. Упаковка из БОПП-пленки сохраняет их полезные свойства на протяжении всего срока хранения, надежно предотвращая проникновение микроорганизмов. Это важно и с точки зрения заботы о природе. Продукты с более длительным сроком хранения реже приходится выбрасывать, а значит, не нужно тратить ресурсы на производство новых.
При этом БОПП-пленка отвечает современному тренду устойчивого развития — она может вторично перерабатываться восемь и более раз.
Одно из пяти
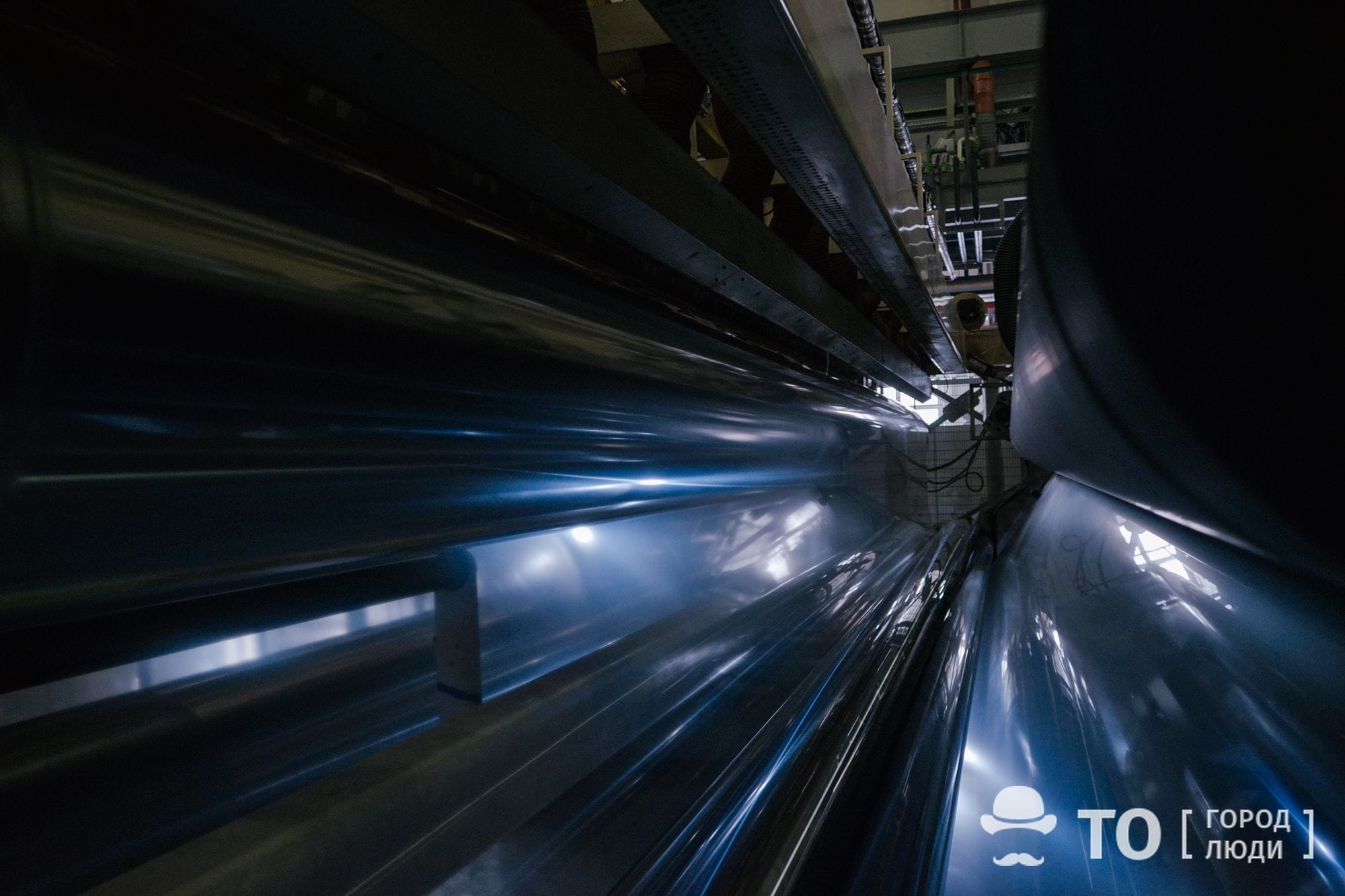
БОПП-пленку в Томске делают на площадке дочернего предприятия СИБУР — «БИАКСПЛЕН Т». Первый завод по производству такой пленки открылся в 2004 году в Курске. В Томске же подобное предприятие начали строить в 2012 году на территории «Томскнефтехима». Спустя год завод был готов, а в ноябре 2013 года состоялось его торжественное открытие.
На сегодняшний день в СИБУРе насчитывается пять площадок, на которых производят почти 60 видов различных биаксиально-ориентированных пленок. При этом томский завод отличается самой широкой линией и возможностью обработки поверхности пленки пламенем.
Сложно представить, что ранее всю пленку привозили из других стран и даже континентов. Не прошло и 20 лет, как БИАКСПЛЕН стал «номером один» по производству БОПП-пленки в России и занял лидирующие позиции в мире. Компания экспортирует пленки в 27 стран мира.
«Сейчас наша линия работает стабильно и выпускает качественную продукцию. И мы стремимся к тому, чтобы все сырье, которое пришло на завод, максимально переработать и выпустить пленку, которую можно передать потребителю. Мы рассматриваем проекты по дальнейшей модернизации линии, с тем чтобы поднять производительность и скорости», — рассказал главный технолог «БИАКСПЛЕН Т» Алексей Бикзантеев.
Какие пленки бывают
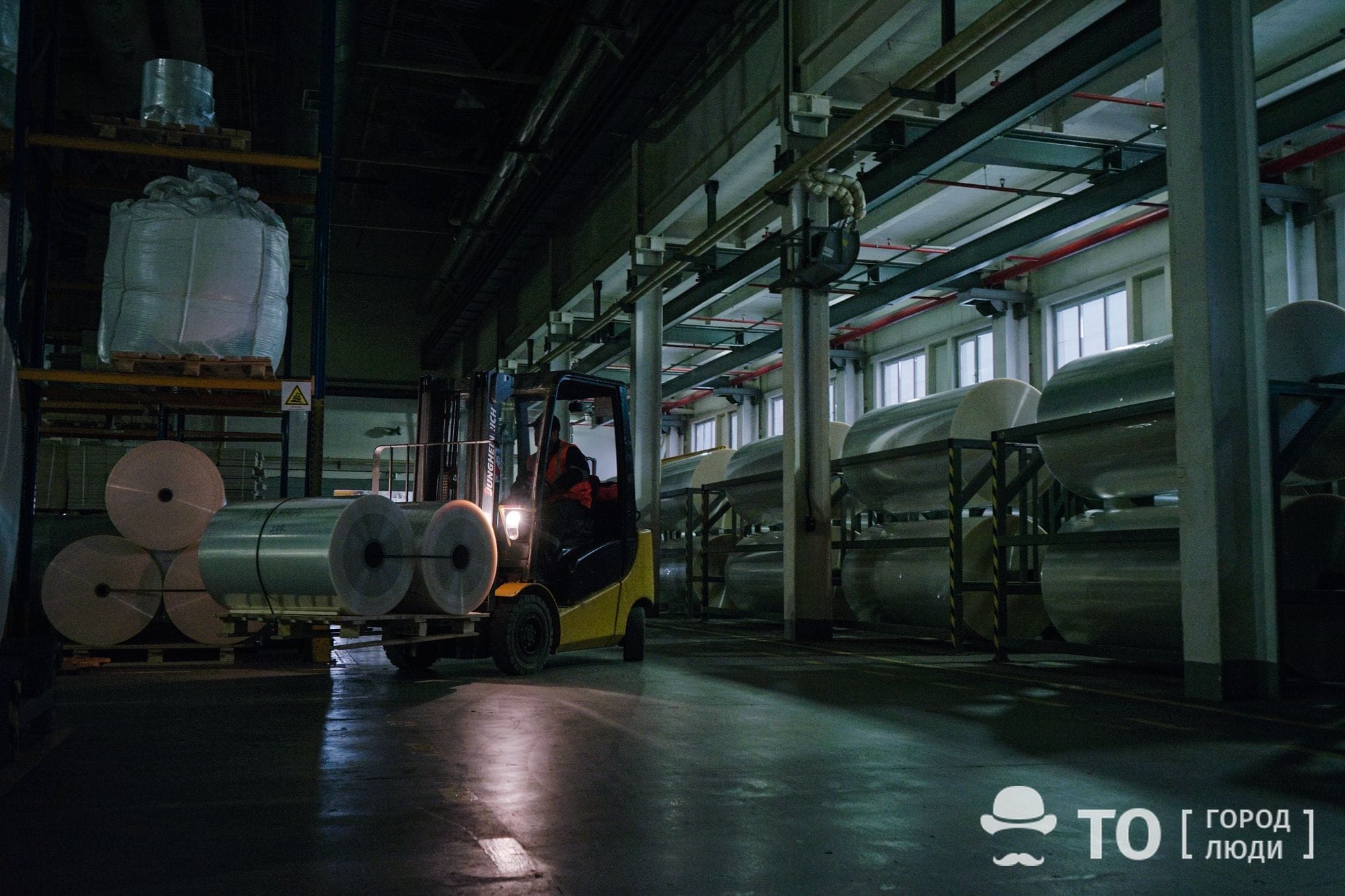
Томская линия рассчитана на выпуск шести видов пленки, которые отличаются друг от друга рядом особенностей.
Так, LOBA — наполненная пленка, которая используется для производства этикеток. Она очень легкая, снаружи может быть любого цвета, но внутри обязательно белая — потому что наполнена микропузырьками. При ее производстве используется добавка, которая при прохождении через конвейер лопается, создавая воздушные пузырьки. Таким образом материал становится толще и одновременно легче.
Пленки типа MGS — матовые, при их производстве нужный эффект достигается добавлением специальных полимеров или матового лака. Такую пленку чаще используют для декорирования.
PGA — с которой и начиналось производство БОПП-пленок на томском предприятии — используется в качестве основы для липких лент (скотча).
HGPL в своих свойствах более интересна. Это термосварная пленка, которая позволяет нанести на себя рисунок и при этом спаивается, образуя шов, который разорвать довольно просто, но не настолько, чтобы упаковка открывалась сама собой. Это возможно благодаря нанесению на внешние слои полимеров, температура сварки которых ниже, чем у полипропилена.
При этом все пленки многослойные. Толщина одного слоя составляет 1 микрон или чуть меньше, тогда как толщина самой пленки — 25 микрон. Именно слоистость пленки позволяет ей приобретать различные свойства.
«Упаковка состоит из многочисленных слоев. Например, упаковка сухариков «Кириешек» («КДВ Групп» является одним из крупнейших потребителей продукции «БИАКСПЛЕН Т») состоит из HMIL и MGS. Металл дает барьерные свойства, что дает более длительные сроки хранения. Алюминий, как и рисунок, наносится между слоями», — рассказывает Алексей Бикзантеев. — Такой конструктор, который помогает привычным продуктам дольше оставаться свежими и сохранять полезные свойства».
Новые свойства пленке можно придать по желанию клиентов, которые приходят в компанию с образом результата, с черновиком идеи. А вот идеи воплощаются в жизнь на базе RND-центров СИБУРа: «НИОСТ» в Томске и «ПолиЛаб» в Сколково. Так вместе с клиентами в компании создаются новые уникальные продукты из полипропилена, который тоже производит СИБУР.
Как уже говорилось, все БОПП-пленки можно успешно перерабатывать. Слои краски, используемые в упаковке, настолько тонки, что они легко устраняются. Алюминия тоже немного — всего 150 граммов на квадратный километр пленки. Однако и его можно отправлять в переработку. Правда, он будет не таким блестящим, но это не мешает делать из него различные детали, которые находятся не на виду (например, колесики для офисных кресел).
Трубы, вода и огонь
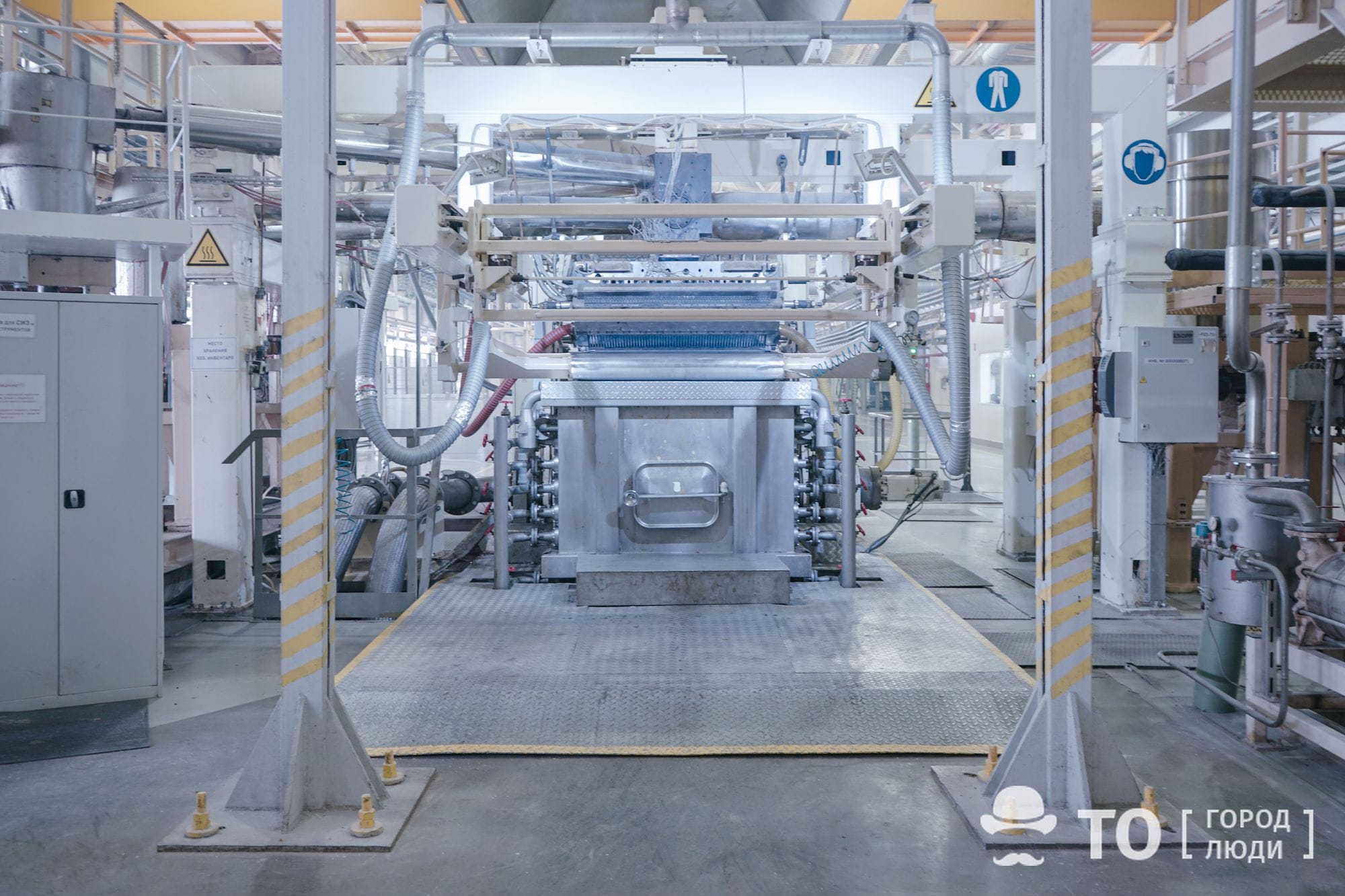
Вся магия превращения гранул полимеров в тонкую и прочную многослойную пленку происходит на производственной линии. Ее длина составляет около 100 с лишним метров. При этом томская линия самая широкая среди всех производств «БИАКСПЛЕНа»: здесь производят пленку шириной 8,7 метра. В Новокуйбышевске — 8,2 метра, остальные — 6,6 метра. Такая ширина снижает себестоимость готовой продукции.
Чтобы из маленьких белых «икринок» стать тонкой и прочной пленкой, полимеры проходят через трубы, воду и огонь — именно в такой последовательности.
Процесс начинается с загрузки полимера в специальные силосы — хранилища сырья. Гранулы в больших мешках попадают в депаллетайзер — своеобразную смесь мясорубки и сепаратора, где их избавляют от деревянных паллет и полимерной упаковки.
Затем гранулы попадают во вращающийся барабан с крупной сеткой и по системе трубопроводов летят в один из трех силосов (всего их пять, но два используются под повторно используемое сырье — об этом позже). Отдельно загружаются добавки — полимеры других видов.
По трубам сырье подается в экструдеры — своеобразные «горячие мясорубки». Всего их пять: один основной и четыре сателлитных, которые отвечают за промежуточные и внешние слои получаемой пленки. То есть, каждый экструдер льет расплав в свой слой.
Пройдя еще несколько производственных этапов, расплав попадает на поливной барабан, где полученную массу к вращающемуся валу прижимает воздушный нож, а после этого пленка охлаждается в ванне с водой. Вода для охлаждения циркулирует в замкнутом контуре. Зимой холодильную установку отключают, воду охлаждают за счет атмосферного воздуха, так как контур частично выведен за пределы комплекса.
Затем пленка, предварительно избавленная от влаги, попадает в зону MDO (machine direction orientaition) — участок продольного растяжения, где горячие барабаны с разной скоростью вращения растягивают ее в длину в 5-6 раз. Далее путь пленки лежит в зону термофиксации.
«Когда полимерные молекулы так сильно растягивают, они хотят вернуться назад. Температура их фиксирует, а потом пленка еще раз догревается», — объясняет процесс Алексей Бикзантеев.
Растяжением в длину процесс не ограничивается. Далее пленка попадает в зону поперечной ориентации, где она становится шире в 10 раз. Здесь пленку нагревают исключительно воздухом, а после ей снова дают «отдохнуть» — немного стянуться и охладиться. На этом же этапе пленку освобождают от кромки, которую обрезают, дробят и подают обратно в экструдер: преобразуют во вторичный гранулят. Выходит, что полимеры практически не могут быть отходами производства: они всегда готовы «превратиться» в новые изделия. Вторичный гранулят снова идет на производство пленки.
На этом манипуляции с пленкой не прекращаются. Далее ее готовят для печати, нанесения клея или дальнейшей металлизации (в зависимости от типа пленки). Для этого поверхность пленки необходимо разрушить — но совсем чуть-чуть, чтобы придать ей необходимую шероховатость, которую нельзя ощутить руками. Делается это двумя способами: коронным разрядом или пламенем. На томской площадке применяют оба метода. Кроме Томска, обработка пламенем в СИБУРе есть только на курском заводе.
Металлизируют пленку на отдельном устройстве. Здесь вал с пленкой помещают в глубокий вакуум. Под ним располагаются «лодочки» с расплавленным алюминием. Емкости с металлом разогревают до 3000 градусов. При такой температуре алюминий начинает испаряться в герметичном корпусе установки, и его пары конденсируются на поверхности пленки. Похожим образом появляются капли воды на крышке кипящей кастрюли. Металлизированная пленка обладает повышенными барьерными свойствами и используется для упаковки продуктов питания, которые требуют герметичного хранения и защиты от света.
«Если вы подходите в магазине к полкам с кормом для животных и не чувствуете запаха, то это очень хорошо. Значит, упаковка выполняет свою задачу и служит барьером для запаха и при этом не пропускает внутрь пакета влагу, воздух, — говорит Ольга Дьяченко, лаборант центральной заводской лаборатории «БИАКСПЛЕН Т».
Из металлизированной БОПП-пленки также делают декоративные этикетки, ее используют при производстве полиграфии. Она применяется для упаковки подарков, цветов — производители отмечают резкий скачок спроса на свою продукцию в преддверии праздников.
Практически готовый продукт подходит к концу производственной цепочки. Пленку наматывают на базисный рулон. Эти огромные шпули или металлические сердечники принимают на себя от 26,8 до 63 км пленки в зависимости от толщины. Затем ее обрезают огромным ножом и ставят новый базисный рулон.
Готовый продукт отправляют на склад, где пленка релаксирует, как говорят технологи, от 12 часов до 6 суток — в зависимости от своего типа. За это время она усаживается, «переживая» все пройденные на производстве испытания.
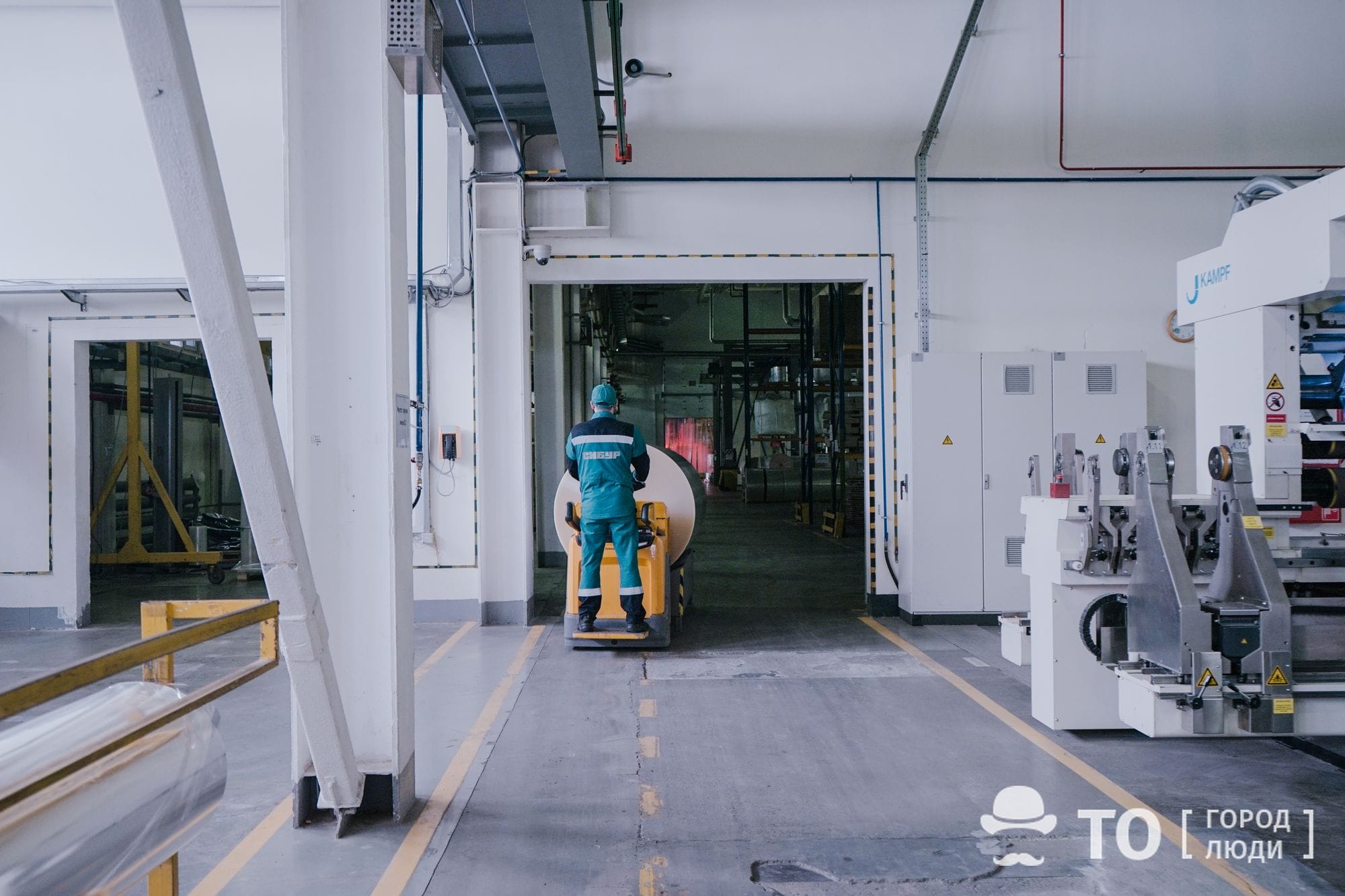
После этого продукт режут под нужды заказчика, и пленка направляется на склад промежуточного хранения.
Автоматы и люди
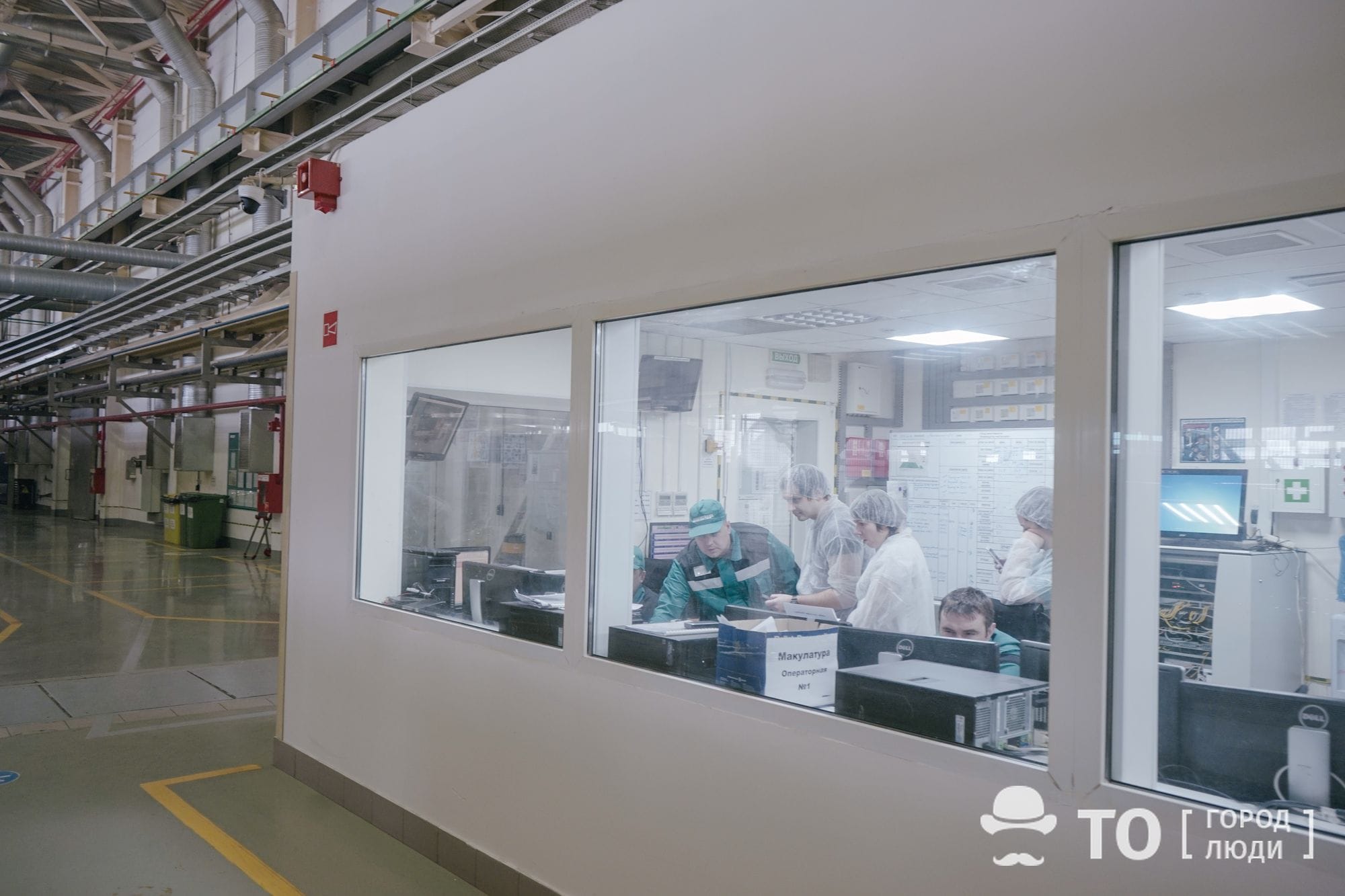
Линия по производству БОПП-пленки предельно автоматизирована. Однако человек все же участвует в производстве. Одни работники загружают сырье в депаллетайзер — эту работу на предприятии отдали на аутсорсинг. Другие следят за качеством пленки в процессе производства, регулируют ее толщину, подкручивая болты на фильере. Также операторы настраивают линию, когда нужно изменить вид выпускаемой пленки.
«Операторы видят всю линию. Вот силоса вращаются в зависимости от заданной рецептуры. Скорость барабана, обороты помпы, обороты экструдеров. В каждом экструдере стоит дозатор, который замеряет: что подается, в каких пропорциях, какие температуры на экструдере, на фильтре, на фильере. Также на пульте видны коэффициенты, с которыми тянется пленка, и многие другие показатели», — объясняет Алексей Бикзантеев.
В случае, если показатели достигают определенных пороговых значений, оператор включается в процесс — меняет температуру или натяжение пленки, чтобы выпустить качественный конечный продукт. При переходе с одного вида пленки на другой операторы проводят ряд манипуляций.
«Если мы выпускаем наполненные пленки, у которых центральный слой белый, то и все трубопроводы, фильтры внутри становятся белыми. Как только мы закончили выпуск данных пленок, мы останавливаем линию, чистим ее, меняем фильтр главного экструдера и прогоняем до полностью прозрачного полипропилена», — объясняет Алексей Бикзантеев.
Контроль качества
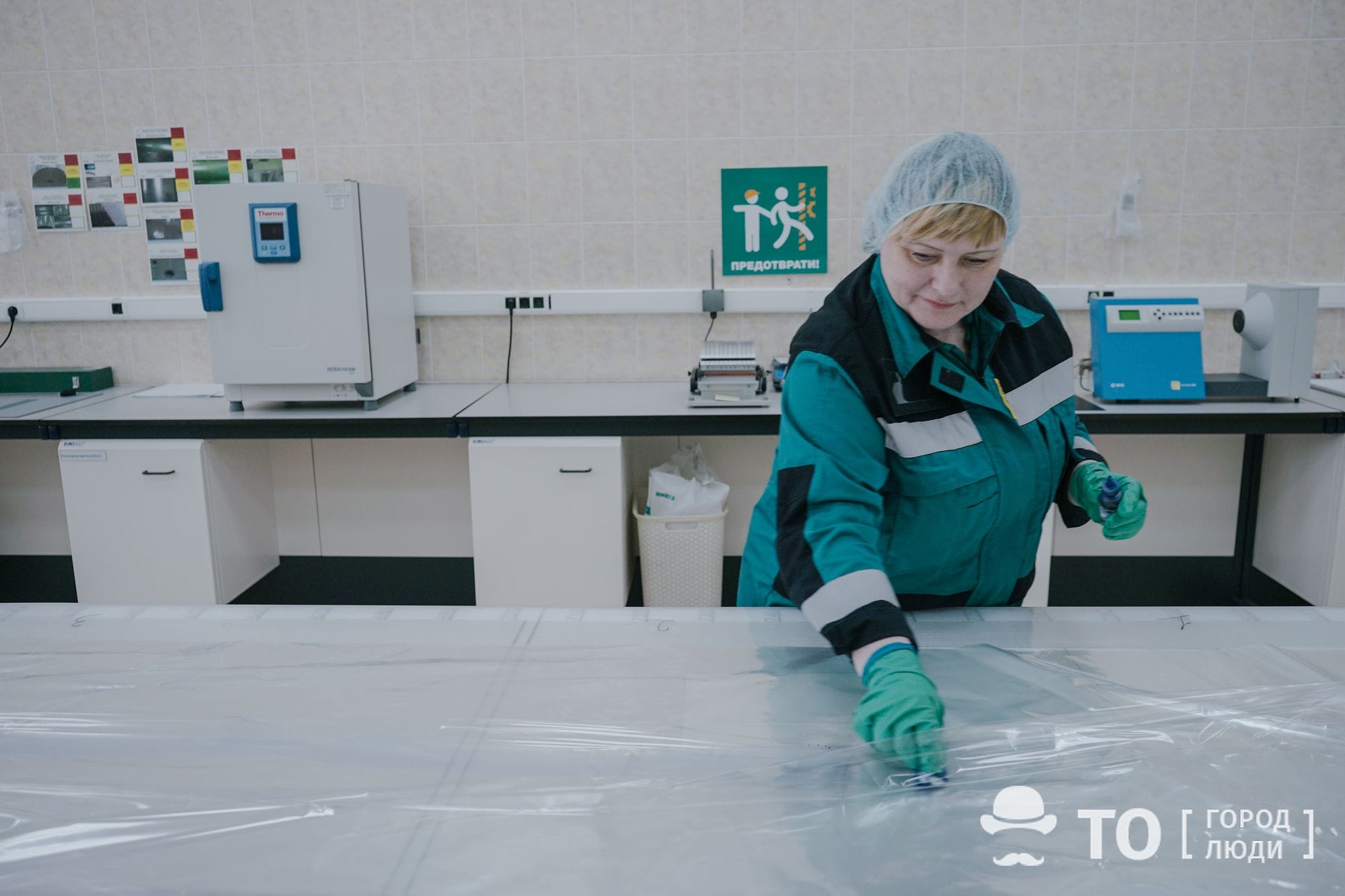
В процессе производства за качеством продукции следят не только операторы. На линии работает прибор, представляющий собой две головки, между которыми идет пленка. Устройство «ездит» по пленке, проверяя ее толщину, и исходя из этого регулирует болты фильеры.
«Если он увидел, что в одном место толщина пленки пошла вверх, то подает нагрев на этот болт; если увидел, что толщина уменьшается, — напротив, снижает температуру», — говорит Алексей Бикзантеев.
Но на этом контроль качества не заканчивается. Каждый рулон готовой продукции исследуют лаборанты: с него срезают образцы, которые тщательно изучаются.
Томскую упаковку могут использовать даже швейцарские сыроделы или бельгийские производители шоколада: продукция «БИАКСПЛЕН Т» сертифицирована на соответствие международному стандарту BRC/IoP по упаковке и упаковочным материалам.
Стандарт признан Глобальной инициативой пищевой безопасности (GFSI) при поддержке ведущих мировых предприятий розничной торговли, производителей продуктов питания и упаковки.
«Здесь определяют толщину, удельный вес, поверхностное натяжение пленки, значения по трению, оценивают внешний вид по нескольким показателям. Проверив физико-механические, оптические, сварные свойства, лаборатория выдает заключение, соответствует ли пленка спецификации клиентов и показаниям технических условий», — объясняет Алексей Бикзантеев.
На основании заключения лаборантов каждый рулон получает паспорт качества. Теперь пленка уже окончательно готова к отправке — и в ее качестве можно быть уверенным!
Текст: Егор Хворенков, Катерина Кайгородова