Нефтехим. Как рождаются полимеры
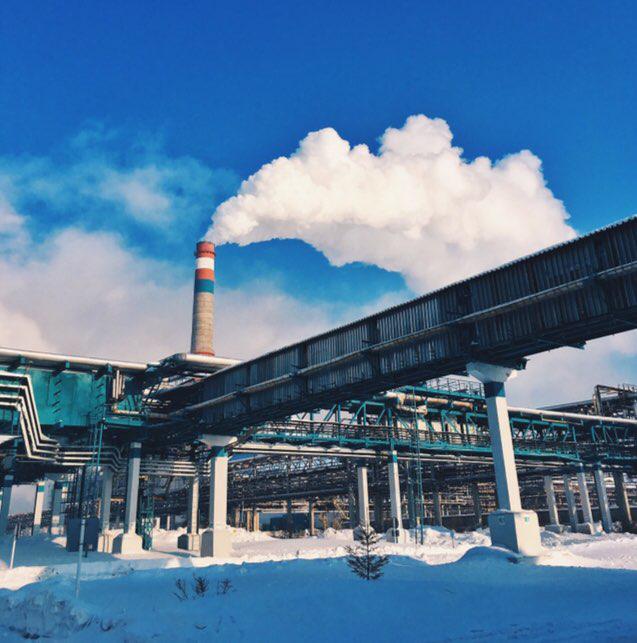
Как производят полиэтилен и полипропилен? Если совсем коротко — то сначала из длинных молекул углеводородного сырья делают короткие фрагменты-мономеры, а затем вновь соединяют их в бесконечно длинные цепочки.
Но во время этого процесса вещества претерпевают удивительные химические превращения. Одни проходят через жар, сильнее чем на Венере, и давление выше, чем в Марианской впадине, другие «варятся» при температуре обычного борща. Тайны создания полимеров раскрывают технологи томского нефтехимического предприятия.
Сырье «из ниоткуда»
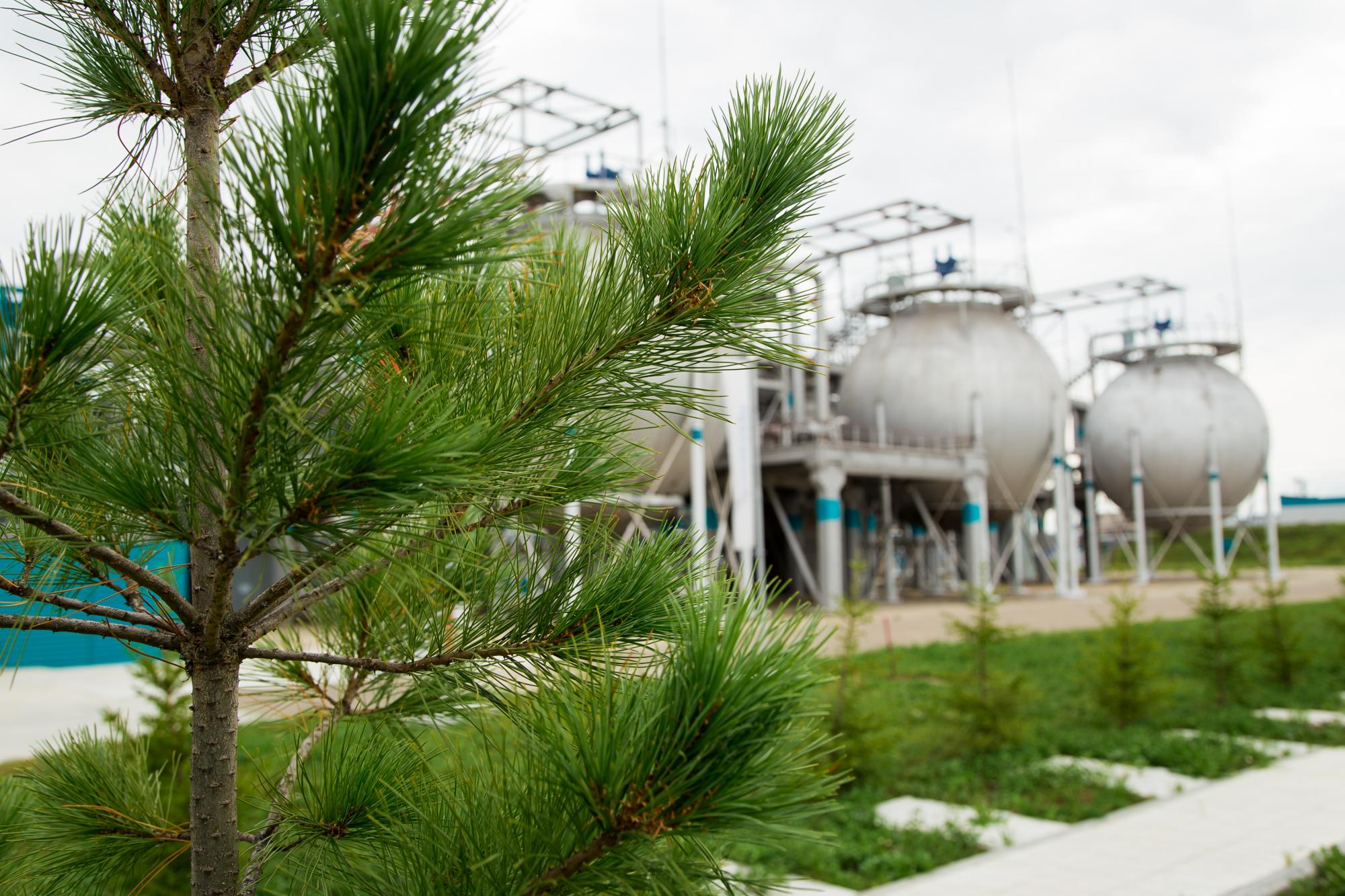
Откуда берутся полимеры? Из газа. А можно ответить словами детской шутки: «из ниоткуда». А все потому, что базовым сырьем для полимеров служит попутный нефтяной газ, который до недавнего времени просто сжигали на факелах при добыче углеводородов.
Вот такие метаморфозы. Нефтяники и газовики добывают сырье, которое потом используется, прежде всего, в качестве топлива в автомобилях и на электростанциях. Однако нефть и газ содержат много побочных примесей, которые и составляют сырье для полимеров. Но для этого примеси нужно выделить и доставить за тысячи километров для переработки. Нефтяники и газовики заняты другим делом, и поэтому попутные нефтяные газы (ПНГ) зачастую просто сжигают на факелах, загрязняя атмосферу.
Газонефтехимические компании приобретают ПНГ для дальнейшей переработки и выделяют смесь газов, которая называется ШФЛУ (широкая фракция легких углеводородов). Вот отсюда и начинают путь полимеры. СИБУР перерабатывает ШФЛУ, разделяя смесь на составные компоненты. На выходе получаются сжиженные углеводородные газы, или СУГ.
Газопереработкой занимаются на восьми заводах СИБУРа в Ханты-Мансийском и Ямало-Ненецком автономных округах. Для дальнейшей транспортировки углеводородные газы превращают в жидкость. На «Томскнефтехим» СУГ приходят в цистернах по железной дороге.
Следующий важный этап преобразования углеводородного сырья — пиролиз, от греческого «пирос» — огонь и «лизос» — распад. В процессе пиролиза и получаются мономеры, которые служат базовым сырьем для полимеров.
Этап 1: из длинных в короткие
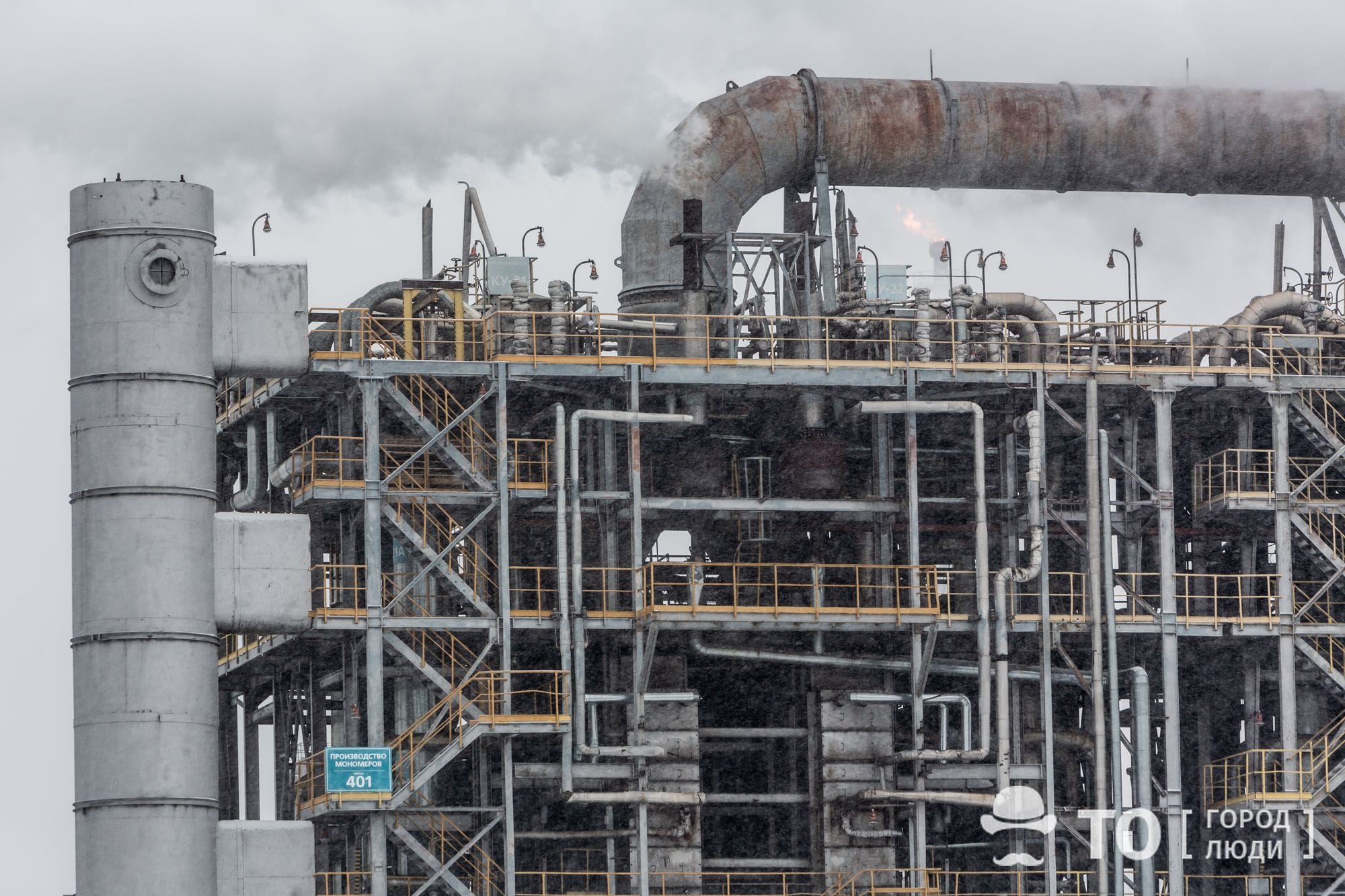
Производственный цикл на «Томскнефтехиме» начинается с изготовления мономеров. Сырье, которое пришло по железной дороге и было залито в специальные хранилища, подают по трубопроводу на печи пиролиза, где нагревают до температуры свыше 800 С. Это почти в два раза горячей, чем на поверхности Венеры, там «всего» 460 С. При нагревании происходит разложение длинных молекул углеводородного сырья на более «короткие» компоненты — мономеры.
Реакция идет в трубчатых печах. На первом этапе сырье смешивается с паром и нагревается до температуры порядка 600 С, дальнейший нагрев происходит в трубах-змеевиках, которые газ пролетает всего за несколько десятых долей секунды.
В процессе пиролиза происходит десятки типов химических превращений, которые идут как параллельно, так и последовательно. Их цель — получить мономеры: этилен и пропилен. Пока «в руках» у нефтехимиков пирогаз — газообразная смесь, состоящая из множества разных компонентов и образовавшаяся в печах пиролиза.
Чтобы вычленить мономеры, пирогазу нужно пройти теперь уже не огонь, но «медные трубы» точно. После выхода из печи он проходит ряд технологических узлов, где отделяется вода, смолы, другие лишние в данном случае вещества. Кстати, их нельзя назвать отходами производства. Так, бутадиен отправляют на завод в Тольятти, где из него делают каучук, а потом шины. Ароматические фракции углеводородов используются при производстве лаков, красок, растворителей и других подобных продуктов. А вода в полном объеме используется в производстве, например, для охлаждения или выработки пара.
Финальный для производства мономеров процесс — разделение смеси на индивидуальные компоненты, происходит в колоннах газоразделения. Здесь, наконец, появляются этилен и пропилен.
Кстати, этилен практически не встречается в природе. Разве что в незначительных количествах образуется в тканях растений и животных как промежуточный продукт обмена веществ. Еще он обладает свойствами фитогормонов — ускоряет созревание плодов.
На установках производства мономеров малолюдно. Львиную долю работы берут на себя автоматизированные системы управления технологическим процессом — АСУ ТП. Самое оживленное место — операторная, где люди следят за параметрами и регулируют их с помощью движков на мониторах своих автоматизированных рабочих мест.
При этом на «Томскнефтехиме» пошли дальше и внедрили на производстве мономеров системы улучшенного управления технологическим процессом — APC (Advanced Process Control). Это мировая практика для управления сложными технологическими процессами. Все могут представить себе, как работает автопилот в авиации: после внесения полетного задания авиатор не вмешивается в процесс управления судном без необходимости, а только контролирует его. Похожим образом выглядит работа системы улучшенного управления технологическим процессом на установке разделения пирогаза. APC самостоятельно контролирует показатели всей установки и ежеминутно в режиме 24/7 перенастраивает их, подбирая и поддерживая оптимальные режимы работы технологических узлов. Также APC в режиме реального времени информирует о качестве продуктов и управляет показателями качества по заранее заданному алгоритму.
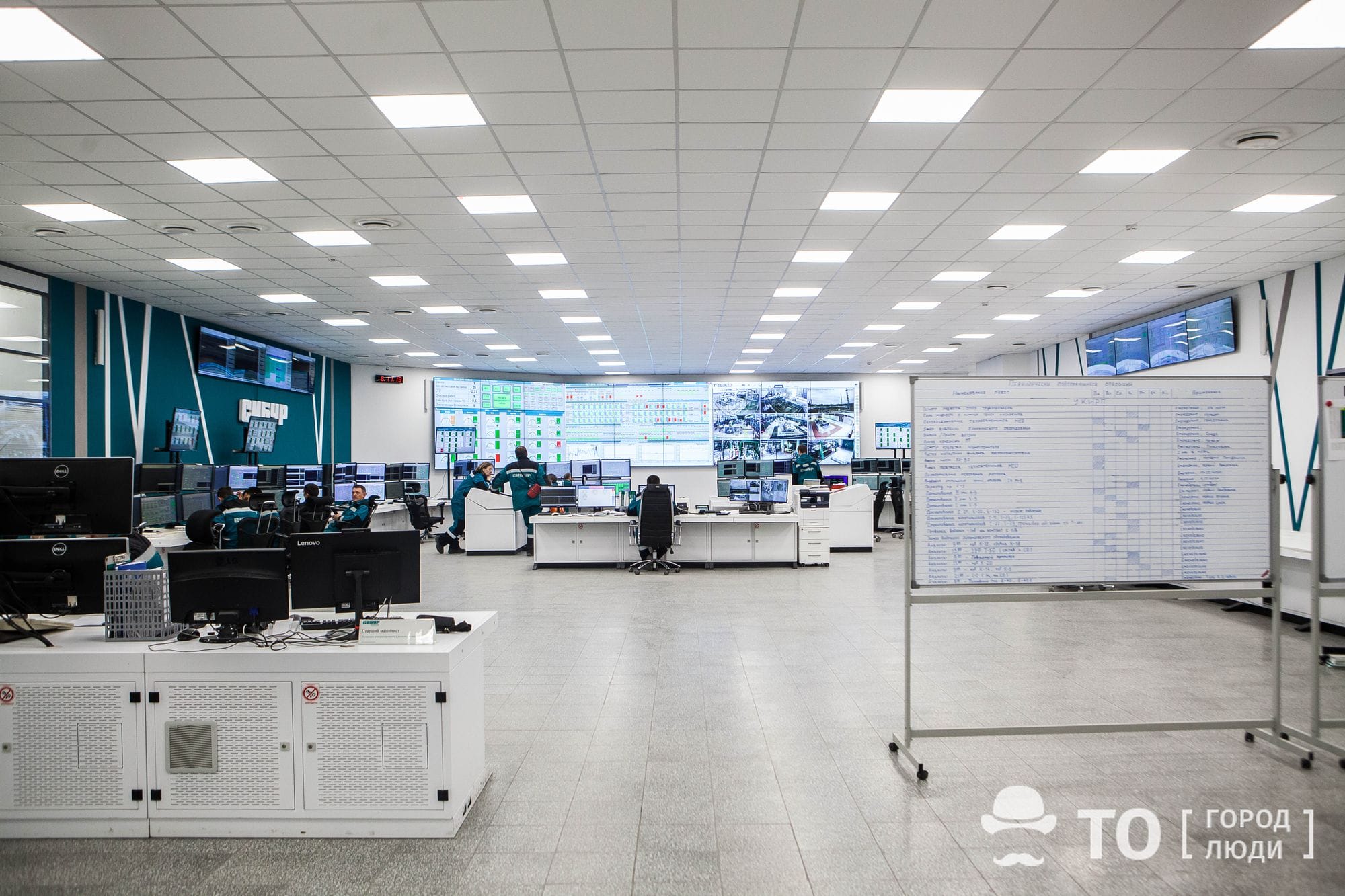
«Да, APC — это своего рода „автопилот“ для технологической установки, но с более развитыми оптимизационными функциями. APC-система управляет установкой, а я как оператор управляю APC-системой», — говорит старший аппаратчик Алексей Котов.
Производство мономеров — непрерывный процесс. За те 20 минут, пока мы наблюдали как оператор «общается» с системой APC, с колонн газоразделения в общей сложности вышло более 15 тонн мономеров. Этилен и пропилен готовы к дальнейшим превращениям.
Основу нефтехимической отрасли составляют предприятия, где имеются пиролизные установки. Мономеры — базовое сырье для дальнейших превращений и получения полимерных материалов.
Установка пиролиза, построенная и введенная в работу в Томске в 1993 году, стала на тот момент крупнейшей отечественной установкой по производству этилена и пропилена. Ее производительность — 300 тысяч тонн в год (считается по проектной мощности выпуска этилена). Цифра по мировым меркам не самая большая, но такой объем полностью обеспечивает потребности полимерных производств «Томскнефтехима» в сырье, есть даже небольшой запас мощности по этилену.
Производство полиэтилена: внеземные условия
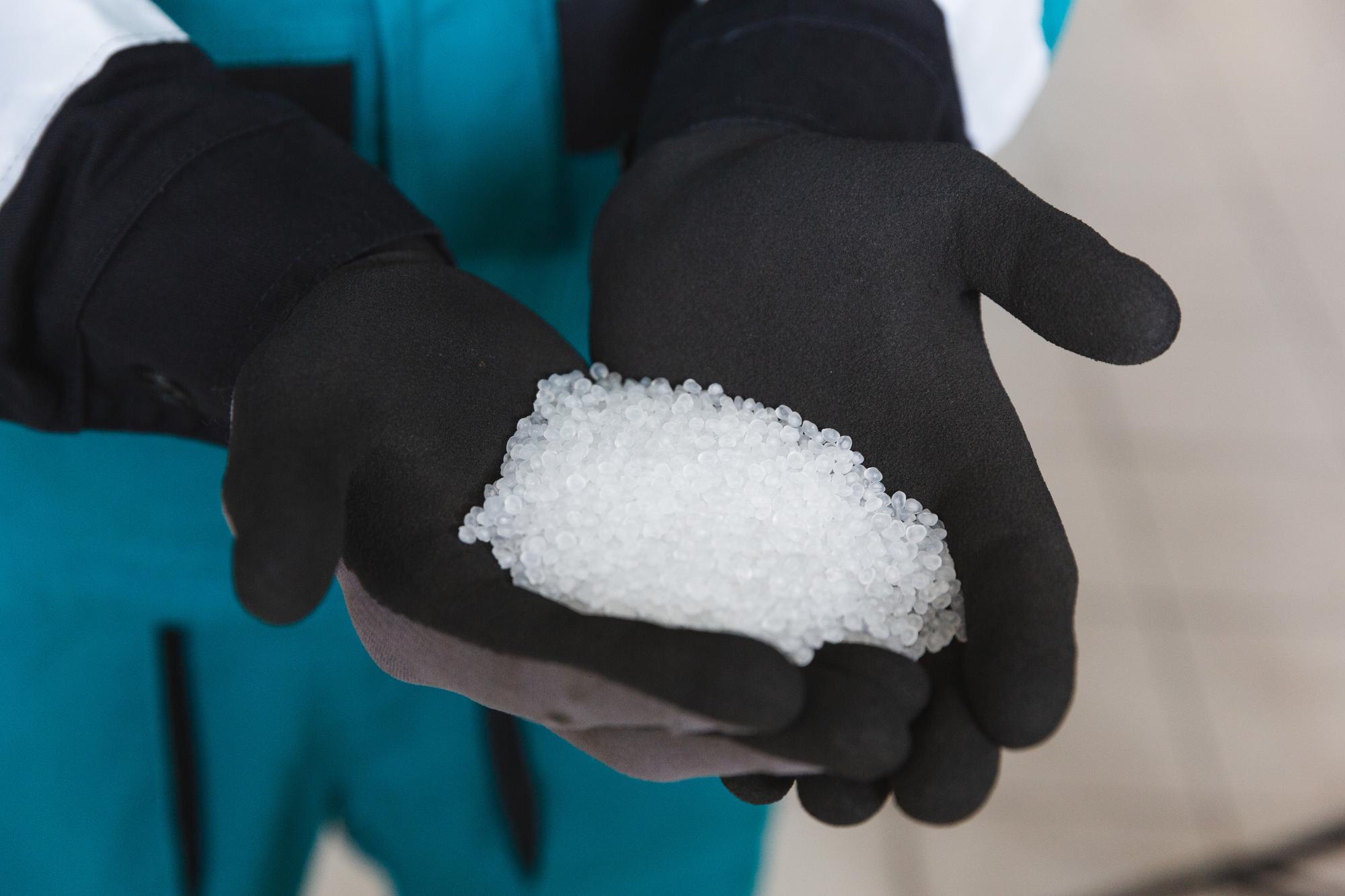
Дальше короткие, но очень ценные молекулы этилена и пропилена отправляют на полимеризацию, в процессе которой мономеры сцепляются между собой, образуя цепочки, содержащие сотни тысяч и миллионы молекулярных звеньев. Отсюда и название «поли», на греческом — «многочисленный».
На «Томскнефтехиме» получают два вида полимеров: полиэтилен и полипропилен. Первый — путем полимеризации этилена, второй соответственно «сшиванием» пропилена.
В СССР промышленный способ получения полиэтилена разработали в 1939 году. Уже через шесть лет из него начали делать бутылки для шампуней и жидкого мыла, которые заменили стеклянные ёмкости. В 1957 году в СССР впервые произвели пакет из полиэтилена, предназначенный для упаковки продуктов.
В 1993 году выпуск полиэтилена был налажен на Томскнефтехиме. Три года назад на этом производстве была завершена комплексная реконструкция — увеличены мощности и расширен ассортимент выпускаемой продукции. Однако на этом развитие комбината не остановилось — технологические процессы оптимизируются и все больше автоматизируются до сих пор.
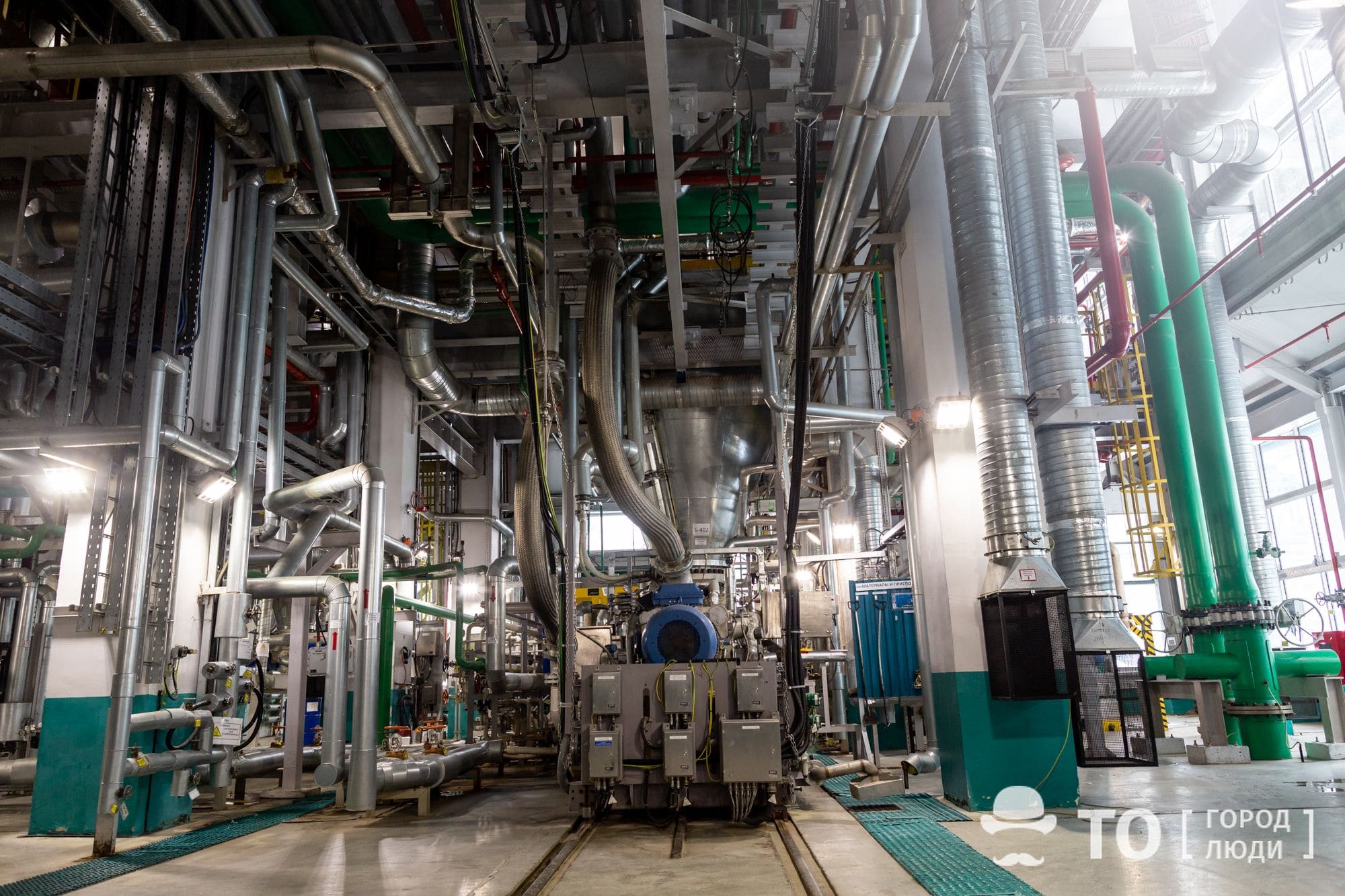
Начнем наше знакомство с производства полиэтилена. На «Томскнефтехиме» получают полиэтилен высокого давления или низкой плотности. Вот такая корреляция.
Для этого используется оборудование с красивым названием — трубчатый реактор идеального вытеснения. Визуально это большая винтовая труба с двойной стенкой, для большей компактности уложенная в слои. На «Томскнефтехиме» реактор полимеризации состоит из трех зон, его протяженность — около двух километров. В реактор подают этилен, где он при высокой температуре и под сильным давлением превращается в полимер. Кстати, в связи с высоким давлением детали реактора полимеризации изготавливают из стали оружейных марок, из таких же делают стволы артиллерийских и танковых орудий.
— Узел компримирования этилена — отсюда все начинается, — поясняет начальник установки полимеризации Александр Чертенков. — Этилен с производства мономеров приходит сюда под давлением 15 атмосфер. Это очень мало для нас, и мы его сжимаем до 2300 атмосфер. Сжатие происходит ступенчато, потому что на каждом этапе необходимо охладить газ.
И уже сжатый этилен отправляется на установку полимеризации. Итак, для процесса «сшивания» полиэтилена нужно три вещи — давление в три раза выше, чем на дне Марианской впадины, а именно 2400 атмосфер, температура, как в жерле вулкана, и химические вещества, начинающие активную цепочку реакции. Их называют инициаторами. Ранее это был обычный кислород, однако теперь наряду с кислородом используются более современные и эффективные инициаторы на основе органических перекисей.
Процесс полимеризации на молекулярном уровне напоминает семейный сериал. Инициатор при нагревании «дарит» разрозненному семейству мономеров свободные радикалы. Это такие частицы, которым больше всех надо: они взаимодействуют с молекулами этилена, а те, благодаря присоединившемуся свободному радикалу, набирают необходимую энергию активации. Молекулы этилена становятся более дружелюбными и способными присоединять новые молекулы этилена, передавая им свою энергию активации, и начиная, таким образом, рост цепи полимера. Получается молекула, которая может содержать до нескольких сотен тысяч мономеров.
С установки полимеризации выходят уже самые настоящие полимеры, правда, еще в виде вязкого расплава. Осталось полимерам обрести форму — стать твердыми белыми гранулами.
Этап 3: из «мясорубки» в силосы
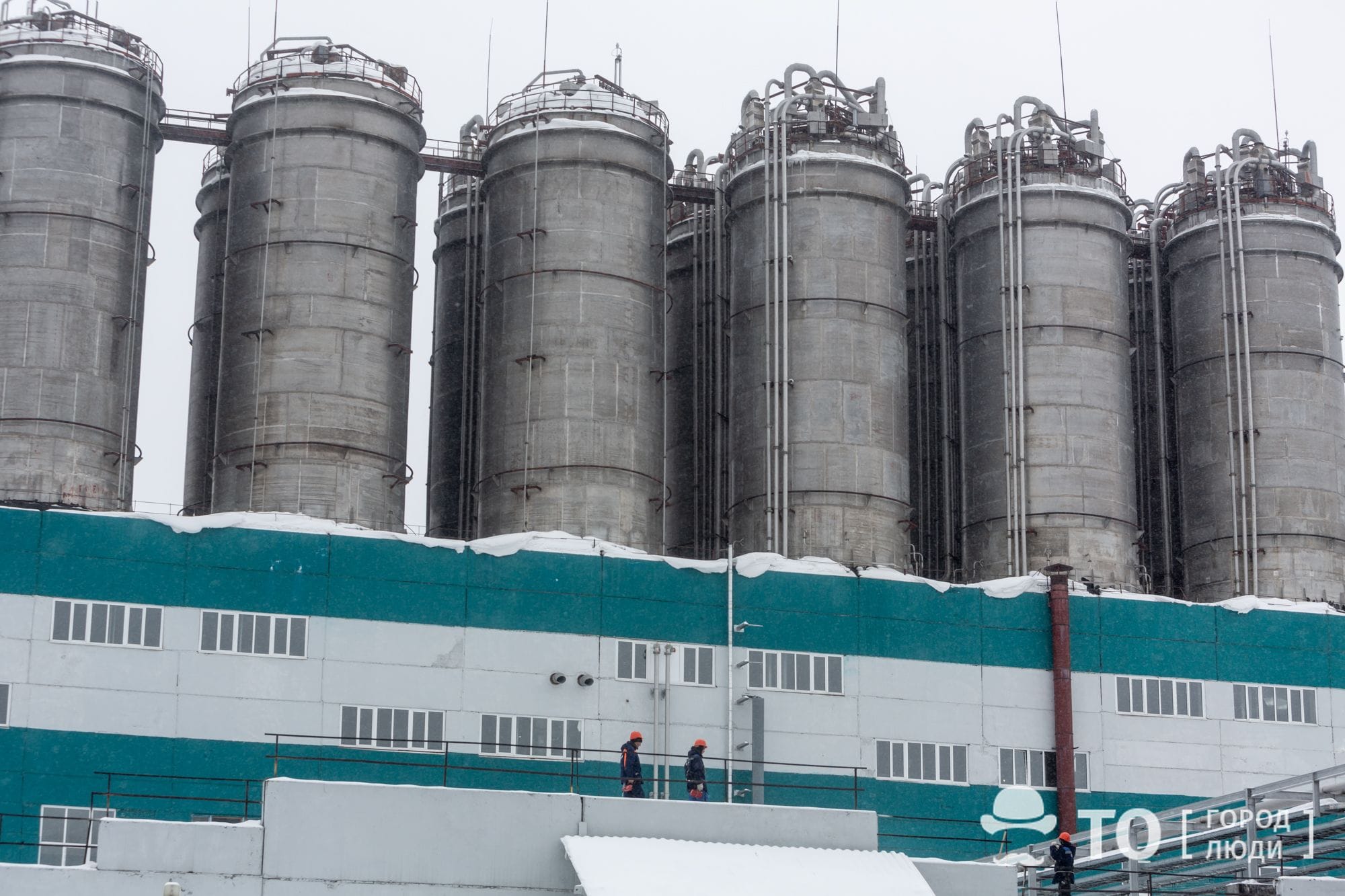
Расплавленный полимер отправляют на экструзию. На этом этапе материал проходит через своего рода мясорубку, которая и формирует из него круглые гранулы. Они выглядят точь-в-точь как готовый продукт, но перед отправкой потребителю гранулят еще около суток должен провести в огромной емкости — «отдохнуть», как говорят нефтехимики. Каждый силос вмещает в себя 600 тонн готового продукта, а всего в сутки на «Томскнефтехиме» производят 820 тонн полиэтилена.
Помните эпизод из известного фильма «Амели», где главная героиня любила запускать ладонь в мешок с чечевицей? Тактильную радость удалось получить и мне, опустив руку в пакет с новенькими гранулами, отобранными для лабораторных исследований на параметры качества. На «Томскнефтехиме» на каждом производстве работает лаборатория, оснащенная высокоточным оборудованием: чтобы «выдать» продукту паспорт качества, обязательный при поставке полимеров переработчикам, нужно исследовать продукт более чем по 15 параметрам.
Фасовка готового полиэтилена и паковка мешков на паллетах тоже полностью автоматизированы. Гранулы фасуют в мешки, за час — более 5000 мешков по 25 килограмм. Потом эти мешки уверенной автоматической «рукой» укладываются на паллеты и за несколько секунд обтягиваются пленкой по технологии stretch hood (англ. «растягивающийся колпак»). Мешки оказываются внутри общей упаковки, тоже, кстати, сделанной из полиэтилена, произведенного на «Томскнефтехиме». Она препятствует проникновению пыли и влаги.
А еще фасовочное оборудование на «Томскнефтехме» автоматически взвешивает мешки с погрешностью до 20 грамм, исключает с помощью металлодетектора попадание в них металлических предметов.
Теперь полимеры ждет путешествие за тысячи километров. Паллеты отправляют автотранспортом, грузят в вагоны, а также на грузовые суда для транспортировки морским путем. Томские полимеры поставляются во все регионы России, в Бельгию, Польшу, Украину, Вьетнам, Китай, Казахстан, Узбекистан и другие страны.
Переработчики превращают полиэтилен в современную упаковочную пленку, изоляционный материал, разнообразные бытовые товары, декоративную упаковку, скотч и даже корпуса бытовой техники и медицинские товары. Полиэтилен, а точнее пленки из него, — незаменимый материал для аграриев. Более 70% российской территории — зона рискованного земледелия. И умные помощники аграриев: тепличные, мульчирующие пленки на основе полиэтилена - помогают получить приемлемый урожай и оптимизировать расходы на возведение теплиц.
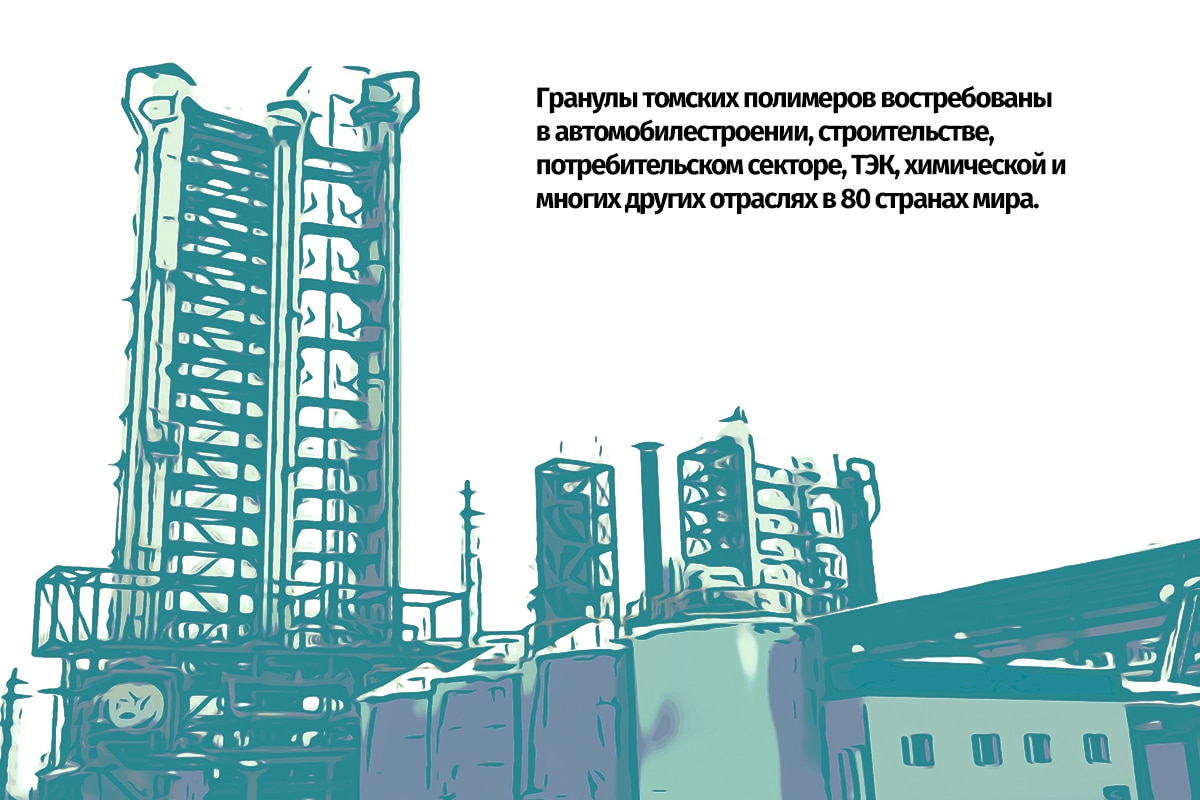
Упаковка из полиэтилена способна продлить срок хранения продуктов на 30%. Ее плюсы — в способности гибко реагировать на различные внешние воздействия, которые влияют на состав и качество перевозимых продуктов. Еще одна из сфер применения полиэтилена — кабельная оболочка. Кстати, у кабельной продукции, которая выпускается в Томске, оболочка — из полиэтилена, выпущенного на «Томскнефтехиме».
Из полиэтилена изготавливают даже медицинские изделия, в частности, медицинские ортезы, которые прекрасно сохраняют форму, при этом они легкие, оптимально гибкие, хорошо пружинят: все, что нужно при восстановлении организма при переломах и растяжениях.
Полипропиленовый «суп»
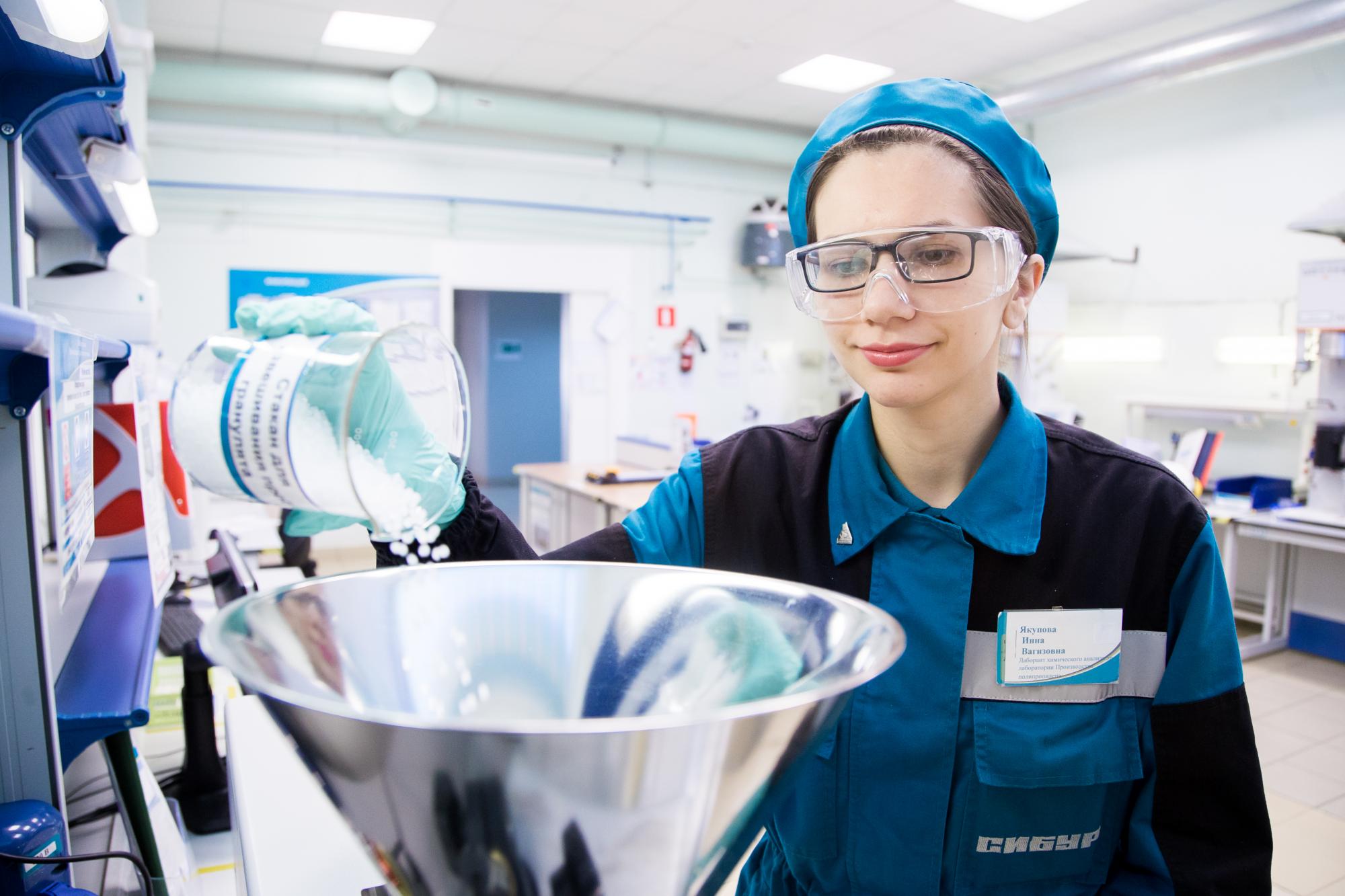
На «Томскнефтехиме» производят еще один вид полимеров — полипропилен, второй по популярности после полиэтилена. Производство полипропилена было первым, построенным на Томском нефтехиме в 1980 году. Также это первая крупнотоннажная установка по выпуску полипропилена в стране, на тот момент ее мощность составляла 100 тысяч тонн в год. Ее появление стало индустриальным прорывом тех лет. Сейчас мощность производства — 140 тысяч тонн в год. В 2016 году на производстве завершилась комплексная реконструкция — обновили ключевое оборудование, расширили возможности предприятия по выпуску специальных высокомаржинальных марок.
Полипропилен, в отличие от полиэтилена, рождается без применения высокого давления и экстремально высоких температур. За процесс полимеризации отвечает катализатор. Благодаря ему молекулы мономеров начинают «дружить семьями» и соединяются друг с другом в длинные полимерные цепочки. Реакция идет при температуре до + 70 С и давлении 7,2 атмосфер, чуть выше той, что в водопроводном кране.
Наряду с базовым сырьем в реактор вводится катализаторный комплекс — специальная смесь, содержащая растворитель, сам катализатор и ряд вспомогательных веществ.
Процесс полимеризации пропилена томские технологи сравнивают с приготовлением мега-борща. К таким образным сравнениям они прибегают, когда нужно очень быстро объяснить суть процесса горожанам, приехавшим на экскурсию.
В качестве реакторов полимеризации используются большие емкости. Каждая емкость оборудована мешалкой и этим напоминает бытовой миксер. К ней подведены трубопроводы, по которым подходят сырье и другие необходимые компоненты. От момента подачи пропилена в емкости до выхода из них суспензии полимера проходит до пяти часов. Пять часов, и «суп» готов. Дальше вся смесь проходит стадии по отделению лишних веществ и превращается в белый сыпучий порошок. Его сушат в несколько этапов и накапливают в так называемых анализных бункерах. Из них лаборанты отбирают пробы для исследования.
Для того чтобы полипропилен был готов отправиться к потребителю, в него необходимо ввести добавки, а также превратить в привычные круглые гранулы. Так, порошок отправляется на экструдеры, где при нагревании превращается в расплав. В него вводят разные добавки, которые помогут переработчикам превратить полимер в изделия с нужными качествами. Это светостабилизаторы, которые защитят изделия от действия света, термостабилизаторы, уберегающие полимеры от воздействия высоких температур, осветлители и другие добавки. Комбинация и дозировка этих веществ помогают создавать широкий ассортимент марок.
После введения добавок расплав продавливается через узкое отверстие фильеры, из которого выходит в виде тонкой нити. Нить погружается в воду, охлаждается и ножами режется на гранулы.
Фасовочные и упаковочные линии идентичны тем, что стоят на производстве полиэтилена
Из полипропилена переработчики по всей стране и за ее пределами производят детали для бытовой техники и автомобилей, канализационные трубы, упаковку для продуктов питания, нетканые материалы, в том числе для детских одноразовых подгузников, емкости и аппараты медицинского назначения.
Так, одноразовое искусственное легкое — оксигенатор, изготавливается в том числе из полипропиленовых волокон и незаменимо в микрососудистой хирургии. Именно одноразовые оксигенаторы, появление которых стало возможным благодаря разработке новых полимеров, исключают инфицирование при сложной операции. Это отмечал главный кардиохирург Минздрава России Лео Бокерия: «Ранее оксигенатор был постоянным, его делали из металла, его дезинфицировали и опять ставили. И наиболее сильные микроорганизмы оставались, шло инфицирование. Пластиковое искусственное легкое перевернуло всю ситуацию».
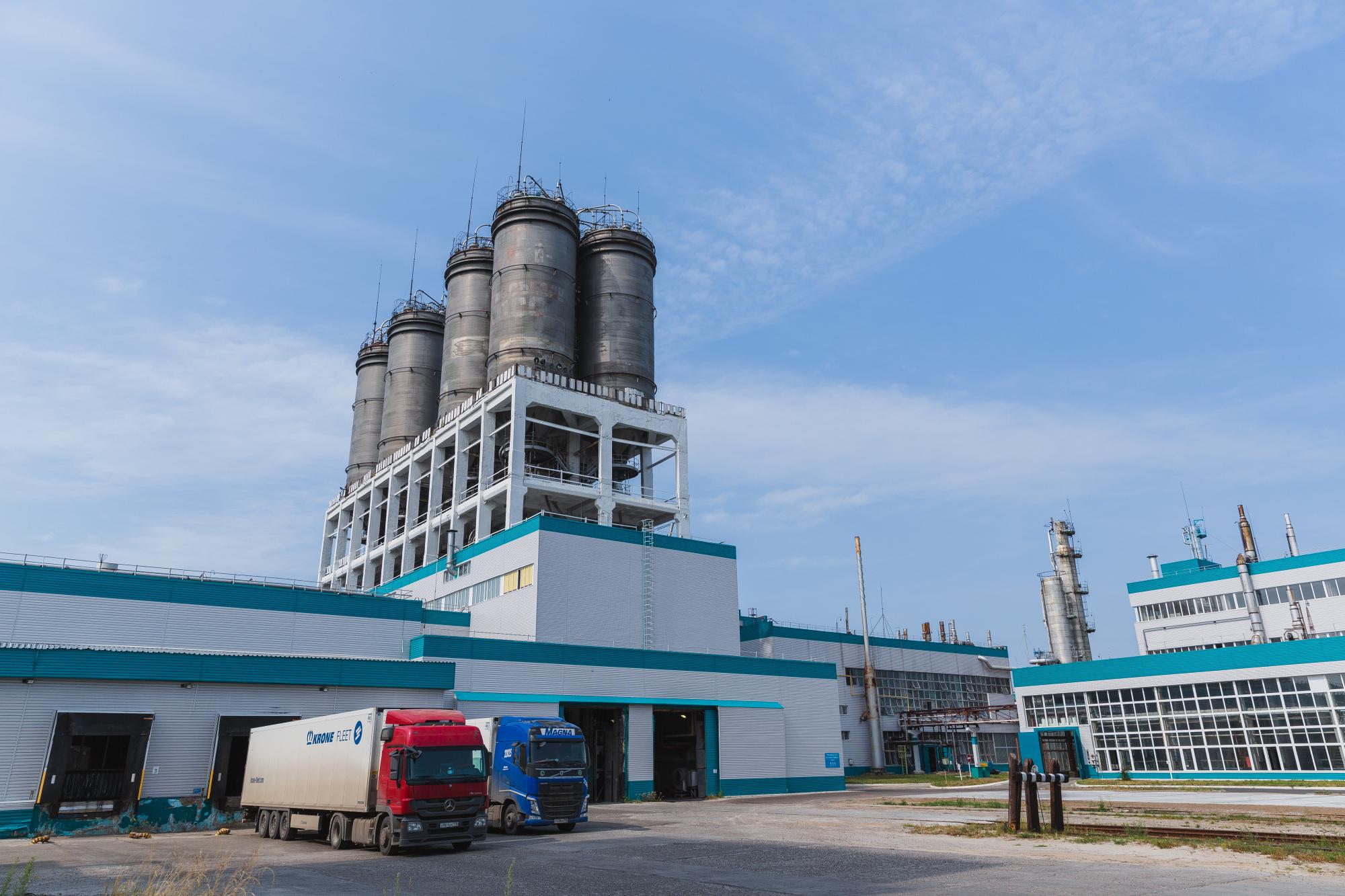
Продукция из полиэтилена и полипропилена, будучи полностью перерабатываемой, имеет серьезное преимущество перед традиционными материалами. Так, продукция из полимеров перерабатывается на 100%; из стекла на 80%; из бумаги на 70%; из алюминия на 80-100%; из стали на 94%.
Полиэтилен и полипропилен дополняют друг друга на рынке современных полимерных материалов. Они прочные и легкие, к тому же устойчивые к воздействиям экстремальных температур, влаги, агрессивных сред, микроорганизмов. Полимеры будто созданы с тем, чтобы отвечать вызовам современной динамичной жизни.